1、引言
航空航天制造業作為高新技術密集型產業,一直代表著世界各國制造業的發展方向,是一個國家制造業實力和國防工業現代化水平的綜合體現;而航空航天高端裝備的服役性能在很大程度上取決于構件的性能。航空航天高性能構件多服役于極端嚴苛環境中,具有超強承載、極端耐熱、超輕量化和高可靠性等特性,對構件的材料、結構、工藝和性能等提出了嚴峻挑戰。近年來,增材制造技術(亦稱3D打印技術)正成為工程、制造、材料、光學等學科的研究熱點,基于增材制造技術可實現復雜結構金屬構件的材料-結構一體化凈成形,為航空航天高性能構件的設計與制造提供了新的工藝技術途徑。增材制造(3D打?。┤驒嗤l展報告“WohlerSReport”指出,航空航天是增材制造技術研發與工業應用最有望獲得突破的領域,增材制造已發展成為提升航空航天設計與制造能力的一項關鍵核心技術,其應用范圍已從零部件級(飛機、衛星、高超飛行器、載人飛船的零部件打?。┌l展至整機級(發動機、無人機、微/納衛星整機打?。?。增材制造技術在航空航天領域的應用主要得益于其在輕量化高性能材料及結構一體化成形領域取得的顯著效益。
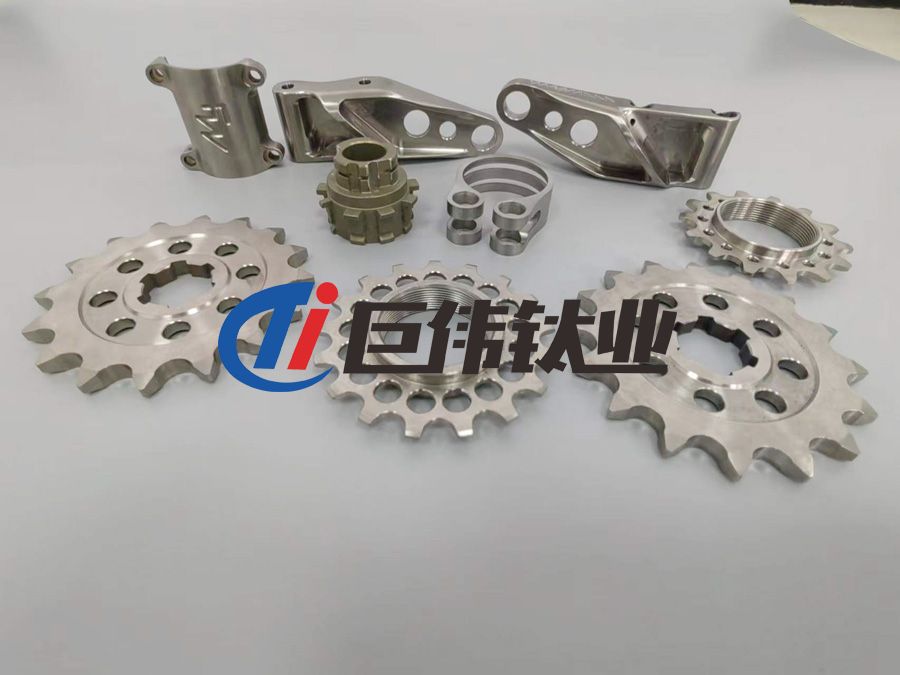
增材制造是國內外科技強國競相發展的一項關鍵核心技術,國家自然科學基金委員會(NSFC)、美國科學基金會(NSF)(2010)將增材制造認定為20世紀制造技術的一項重大創新?!懊绹圃欤簢以霾闹圃靹撔卵芯吭海ǎ危粒停桑桑保?013年)、《德國工業4.0戰略計劃實施建議》(2013年)將增材制造技術作為新一代革命性技術以及未來科研和產業發展的新增長點而加以培育和支持。中國政府在《中國制造2025》(2015年)、《國家增材制造產業發展推進計劃(2015—2016年)》(2015年)、《國務院關于印發“十三五”國家戰略性新興產業發展規劃的通知》(2016年)、《加強“從0到1”基礎研究工作方案》(2020年)等科技強國和制造強國戰略行動綱領中,前瞻性地布局了增材制造關鍵核心技術,打造及完善增材制造產業鏈,力求占領技術發展戰略高地。
基于激光技術實現高熔點難加工金屬、合金及金屬基復合材料構件的直接成形,是增材制造技術研發領域最為熱門的方向之一;而基于激光與粉末的增材制造技術已形成兩類典型成形工藝,并表現出兩種不同的發展方向:一類是基于噴嘴自動送粉的激光熔化沉積(LMD)技術或激光立體成形(LSF)技術,它利用高能激光熔化同步供給的金屬粉末,采用特制的噴嘴在基板上逐層沉積成形構件。LMD沉積層厚度為毫米尺度,制造速度快,適合制造大型構件,這是該技術應用及發展的主要方向。此外,LMD成形件通常需要進行后續精整加工,以達到結構控形及尺寸精度的要求。另一類是基于粉床自動鋪粉的選區激光熔化(SLM)技術或激光粉床熔融(LPBF)技術,它利用高能激光熔化處于松散狀態的粉末薄層(厚度通常為20~50μm),基于粉床逐層精細鋪粉、激光逐層熔凝堆積的方式,成形任意復雜形狀的高致密度構件。SLM技術成形精度高,對特殊復雜結構(如懸垂結構、薄壁結構、復雜曲面、空間點陣等)制造的適用程度高,其發展方向是實現中小型復雜構件直接精密凈成形。不論是面向大型金屬構件的LMD技術,還是面向中小型精密金屬構件的SLM技術,均為高性能復雜結構金屬構件的低成本、短周期、凈成形制造提供了一體化解決方案,在航空航天等領域具有廣闊的應用及發展前景。對比金屬激光增材制造技術的國內外發展歷程及現狀可知,德國、美國等國在激光增材制造的原創性工藝技術、核心光學部件(如激光器、振鏡等)、高性能金屬粉末材料上有較深厚的研發積累,而我國的金屬激光增材制造技術發展水平近年來顯著提升,金屬增材制造裝備、材料、工藝、軟件等朝著國產化、產品化、專業化方向不斷推進,特別是在航空航天重大需求的牽引下,高性能大尺寸金屬構件激光增材制造的工藝研發及應用水平已走在了國際前列。近年來,在國家航空航天重大需求和前沿科學探索的雙重驅動下,金屬構件激光增材制造研究在材料、結構、工藝、技術、性能/功能等多方面呈創新發展之勢。從航空航天領域日益增強的工程需求出發,面向極端嚴苛環境的航空航天構件的服役性能要求不斷提升,故要求構件的強度、韌性、剛度等力學性能指標顯著提高,并要求構件具有防熱、隔熱、減振、抗輻射等特殊功能。只有通過創新發展增材制造的新材料、新結構、新工藝,才能有望獲取顛覆性的性能和功能,滿足國家航空航天領域重大工程的需求?;谇把乜茖W探索與發展角度,發表于Sciencs的《金屬的未來》(2011年)一文指出:現代工業要求結構材料具有高的強度、斷裂韌性及剛度,同時盡可能減重,即要求材料的比強度更高;在提高材料比強度的同時,不損害其韌性和塑性等性能,對提高材料的工程應用競爭力至關重要。同時,Sciencs論文預測指出,多材料(如具有可控增強結構的金屬基復合材料)是解決傳統金屬材料比強度和比剛度低、耐蝕性差等劣勢的重要途徑。與前沿科學探索相一致,隨著現代航空航天工業的快速發展,以鋁、鈦合金為代表的輕質高強合金、以Ni基高溫合金為代表的承載耐熱合金,是各國新材料研發計劃中重點發展的材料之一,也是激光增材制造中重要的應用材料?,F代航空航天構件需同時滿足輕量化、高性能、高可靠性、低成本等一系列苛刻要求,且構件的結構更為復雜、設計制造難度更大。通過創新和發展航空航天典型鋁、鈦、鎳基構件激光增材制造控形與控性關鍵技術,既體現了選材上輕量化、高性能的發展方向,又凸顯了增材制造技術本身精密化、凈成形的發展趨勢,可實現材料-結構-性能的一體化增材制造以及增材制造技術在航空航天上的重大工程應用。
本文針對航空航天領域三類典型應用材料(即鋁、鈦、鎳基合金及其金屬基復合材料)、四類典型結構(大型金屬結構、復雜整體結構、輕量化點陣結構、多功能仿生結構等),闡述了近年來國內外在面向激光增材制造的新材料制備、新結構設計、成形件控形與控性、高性能/多功能突破、航空航天領域典型應用等方面的研究進展,提出了高性能金屬構件激光增材制造的宏/微觀跨尺度形性協調機制,并就激光增材制造技術未來在材料、結構、工藝、性能等方面潛在的研究方向作一點思考與展望。
2、面向激光增材制造的高性能金屬材料
2.1激光增材制造鋁合金及鋁基復合材料
對于激光增材制造而言,鋁基材料是典型的難加工材料,這是由其特殊的物理性質(低密度、低激光吸收率、高熱導率及易氧化等)決定的。從增材制造成形工藝角度看,鋁合金的密度較小,粉體流動性相對較差,在SLM成形粉床上鋪放的均勻性較差或在LMD過程中粉末輸運的連續性較差,故對激光增材制造裝備中鋪粉/送粉系統的精度及準確性要求較高。未熔化前,鋁對CO2激光的初始吸收率僅為9%,而其熱導率高達237W/(m·K),為鐵的3倍、鈦的16倍,通常的低功率CO2激光難以使鋁粉體發生有效熔化。即便使用短波長、高功率光纖或Nd∶YAG激光使鋁粉發生初始熔化,其高的熱導率又將使輸入熱量急速傳遞而消耗掉,導致熔池溫度降低、熔池內液相的黏度增加;同時,高溫下鋁熔體與氧具有很強的親和力,而激光成形腔體內即便通過抽真空或通保護氣體使氧含量降至10×10-6(體積分數)以下,系統內殘余的氧元素也會在熔體表面形成氧化膜,降低熔體的潤濕性和鋪展性,進而將促進金屬粉末SLM增材制造特有冶金缺陷-----“球化”效應及成形件內部孔隙、裂紋等的發生,從而顯著降低激光增材制造構件的成形性能。
相對于鈦基、鎳基等金屬材料對SLM和LMD兩種工藝表現出的廣泛適用性,鋁基材料激光增材制造的研究工作及應用驗證較多集中在SLM工藝上。目前基于SLM成形的鋁合金及鋁基復合材料如表1所示。其中,AlSi10Mg和AlSi12等Al-Si合金具有良好的鑄造性能和焊接性能,故對SLM這類經歷粉末熔化/凝固冶金熱物理過程的增材制造工藝表現出了良好的成形性能。激光增材制造Al-Si系合金的顯微組織演變規律和調控機制較為一致:在激光非平衡快速凝固條件下,SLM成形AlSi12呈現為微細的富鋁胞狀組織,殘余硅顆粒在晶界析出;經熱處理后,顯微組織將發生一定程度的粗化,硅組元從晶胞中繼續析出并形成硅顆粒。SLM成形AlSi10Mg表現出與AlSi12相似的顯微組織特征及演變規律。需要指出的是,析出硬化AlSi10Mg合金在SLM激光快速凝固過程中并沒有析出Mg2Si沉淀相,但細化的亞微米胞狀組織仍為激光成形件提供了較高的強度。激光增材制造工藝參數(如激光光斑尺寸、激光功率、掃描速度、掃描間距、鋪粉厚度等)及掃描策略、成形方向、成形件布局方式等均可顯著影響構件的成形質量、顯微組織及最終的力學性能。為綜合評估SLM諸多工藝參數的耦合作用,可通過“激光線能量密度”(λ=P/v)綜合“激光功率P”和“掃描速率v”的影響,且可通過“激光體能量密度”(ε=P/(vhd))進一步耦合“掃描間距h”和“鋪粉厚度d”的影響,分別用以調控“線成形質量”和“體成形質量”,為金屬構件SLM激光增材制造的精確化、穩定化控制提供關鍵工藝參數指標,并為激光成形件內部顯微組織、冶金缺陷、殘余應力及成形性能的“由線及體”的立體控制提供關鍵方法及科學機理。AttAllah小組研究了SLM工藝參數對AlSi10Mg致密化行為的影響規律,發現采用較高的激光功率、較低的激光掃描速度和較小的掃描間距可有效減少或消除成形件內部的孔隙,且AlSi10Mg合金獲得良好SLM成形性能所需的體能量密度閾值在60~75J/mm3之間。ThijS等[24]學者在SLM激光掃描策略優化的研究中發現:當采用島狀掃描策略進行SLM成形時,Al-Si合金的晶體織構明顯減弱,沿著成形方向形成較弱的〈100〉立方織構,成形件各方向的拉伸強度主要受織構的影響,表現為各向同性;然而成形件的韌性卻表現為各向異性,這是由于微觀組織的各向異性使得裂紋通常沿著熔池邊界形成,故平行于掃描方向的延伸率更高。減小掃描路徑長度,可降低相鄰熔道間的熱量損耗,熱量積累更均勻,溫度梯度減小,可降低激光成形件的殘余應力。Wang等研究了掃描策略對SLM成形AlSi10Mg力學性能的影響規律,發現島狀掃描成形試樣的抗拉強度和延伸率高于相同工藝參數下線性掃描成形試樣。
表1激光增材制造鋁合金及其復合材料的力學性能
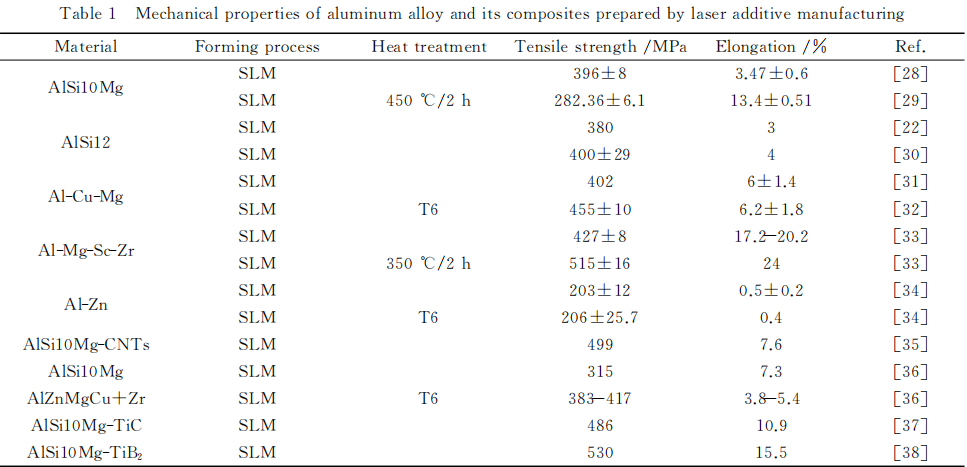
如表1所示,Al-Si系合金因其鑄造鋁合金的材料本質,雖然采用經過優化的激光增材制造工藝進行制備,但抗拉強度很難突破400Mpa,從而限制了其在航空航天等領域服役性能要求更高的承力構件上的使用。為進一步獲得更高的力學性能,近年來Al-Cu、Al-Mg和Al-Zn等鋁合金體系也被用作SLM成形材料,但這類鋁合金中較高的合金元素含量和較寬的冷卻凝固溫度范圍,使得沉淀強化合金在激光增材制造過程中易形成裂紋甚至發生開裂;且相對于鋁元素,鎂和鋰等合金元素更易在高能激光的高溫作用下發生氣化蒸發,從而影響成形件的成分穩定性及力學性能。Zhu研究小組發現:激光體能量密度對Al-Cu-Mg(2024鋁合金)SLM致密化行為具有顯著影響,當激光體能量密度高于340J/mm3這一閾值時,可獲得無缺陷、無裂紋的高致密度(相對密度為99.8%)成形件。激光成形顯微組織由微細過飽和的胞狀晶-樹枝晶復合結構組成,在細晶強化機制和固溶強化機制的協同作用下,成形件的抗拉強度可達402Mpa,屈服強度可達276Mpa。2024鋁合金等高強鋁合金較難通過激光增材制造工藝獲得預期的高性能,這主要是由于該材料的成分和物性參數并非是專門為激光增材制造設計的。因此,對于激光增材制造高強鋁合金而言,成分、物性參數、相變的設計及調控尤為重要。近年來,人們設計了專用面向激光增材制造的稀土元素鈧改性增強的Al-Mg-Sc-Zr合金粉末,其激光成形件的力學性能有望獲得突破性提升。SLM成形Al-Mg-Sc-Zr合金直接沉積態試件的組織呈典型的雙峰晶粒分布:在熔池邊界處,以初生Al3(Sc,Zr)相和細小的Al-Mg氧化物作為形核點,形成等軸晶區;在熔池中部形成沿溫度梯度生長的柱狀晶區。激光增材制造Al-Mg-Sc-Zr合金力學性能的躍升需輔以適當的后續熱處理工藝。經325℃/4h時效處理后,SLM成形Al-Mg-Sc-Zr合金中的晶粒無明顯粗化現象,其基體內可原位析出尺寸為5~10nm的二次Al3(Sc,Zr)相,該析出相與基體保持共格界面,可有效釘扎位錯,具有顯著的納米彌散強化效應,可顯著提升成形件的綜合力學性能(抗拉強度高于500Mpa,延伸率超過10%)。制備鋁基復合材料是鋁合金強韌化的重要途徑。鋁基復合材料兼具輕合金與陶瓷、纖維等增強體的優良特性,具有高的比強度、比模量及體積穩定性,并具有耐高溫、抗磨損及抗氧化等優異的性能以及材料可設計性。激光增材制造鋁基復合材料在選材上突出“多相材料可設計性”,在增材制造工藝上強調“高可控性”,在使用成效上則凸顯“高性能/多功能”,這也代表了增材制造技術的重要發展方向。納米陶瓷增強和原位陶瓷增強可有效改善陶瓷/金屬界面的潤濕性及結合性,抑制界面上的微觀孔隙及裂紋,提升激光成形件的力學性能。筆者研究團隊基于SLM過程中高能激光對納米陶瓷微粒完全熔化及潤濕的成形機制,實現了四類陶瓷(包括TiC、SiC碳化物,TiB2硼化物,AlN氮化物,Al2O3氧化物)、兩類增強方式(包括納米彌散增強和原位析出增強)的鋁基復合材料的激光增材制造,發現了高能激光輻照特有的加熱方式(具有逐點逐行區域化掃描特征)、能量特點(瞬態升溫可達5000°C以上)及冶金機制(激光快速凝固速率高達106K/S)可使鋁基復合材料的納米/原位陶瓷增強相具有環狀、條帶狀、層片狀等新穎的微觀結構(如圖1(a)、(b)所示),這些新穎的微觀結構顯著區別于傳統鑄造或粉末冶金鋁基復合材料的顆粒狀增強結構;揭示了激光增材制造過程中高度非平衡熔池內的Marangoni流、溫度場、速度場、溶質場等冶金熱力學和動力學行為對納米/原位陶瓷增強相形成、晶體生長和空間分布起決定性作用;發現了激光作用下形成的具有獨特顯微組織及分布的納米/原位陶瓷增強相與鋁基體間具有共格界面且兩相原子匹配性強,在納米/原位陶瓷增強相的作用下,鋁基體可發生顯著的等軸晶化及晶粒細化(如圖1(c)所示),基于增強相與基體相的顯微組織調控可使激光增材制造鋁基復合材料構件的強度和斷裂韌性獲得協同提升。
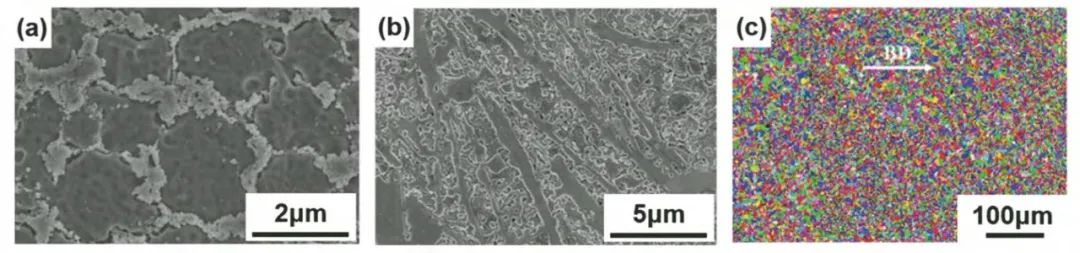
圖1激光增材制造鋁基納米/原位復合材料的顯微組織調控。(a)環狀TiC納米增強相;(b)條帶狀Al4SiC4原位增強相;(c)TiB2增強作用下鋁基體細化的等軸晶組織
對于不可焊6系和7系鋁合金等激光增材制造裂紋敏感性特別強的材料,納米顆粒改性和增強的策略是顯微組織改善的良策,可改善激光增材制造試件的成形性能和力學性能。對于6系和7系鋁合金來說,在SLM激光快速凝固過程中,溶質易在凝固界面附近的熔體中偏析,引起顯著的成分過冷,凝固組織易呈樹枝狀晶長大,并在凝固組織間形成較長的液相通道;當凝固溫度進一步降低時,液相凝固收縮產生孔隙、裂紋甚至熱撕裂。MarTin等學者在Nature上發文指出,他們通過納米顆粒改性增強的策略解決了上述問題;他們根據結晶學信息選擇納米鋯粒子作為成核劑,然后通過靜電附著將其組裝到7075和6061系鋁合金粉末顆粒表面,最后采用SLM技術成形。他們發現,在激光熔池中鋯顆粒與鋁基體發生反應生成的Al3Zr,提供了大量低能量勢壘非均質形核位點,促進了微細等軸晶的形成,從而降低了凝固收縮應力的影響,獲得了具有均勻等軸晶組織、無裂紋且強度高的鋁基構件,如圖2所示。此外,航空航天等極端嚴苛的服役環境對鋁合金構件的強度、韌性、模量、剛度等性能指標提出了嚴格要求,因此,高體積分數的陶瓷增強鋁基復合材料的制備具有重要的工程應用價值。NatureCommunicaTionS報道了Lin等學者在制備納米TiC增強鋁基復合材料方面的工作,他們首先制備了具有高體積分數(最高可達35%)的納米TiC增強鋁基納米復合粉末,然后利用SLM工藝實現了塊體鋁基復合材料的制備,成形件的屈服強度高達1000Mpa,塑性超過10%,楊氏模量約為200GPa,這是目前結構金屬材料中比楊氏模量、比屈服強度最高的材料;這些性能的提升主要歸因于高密度分散的納米增強顆粒、納米顆粒與鋁基體間的強界面結合以及激光作用下形成的超細晶粒。
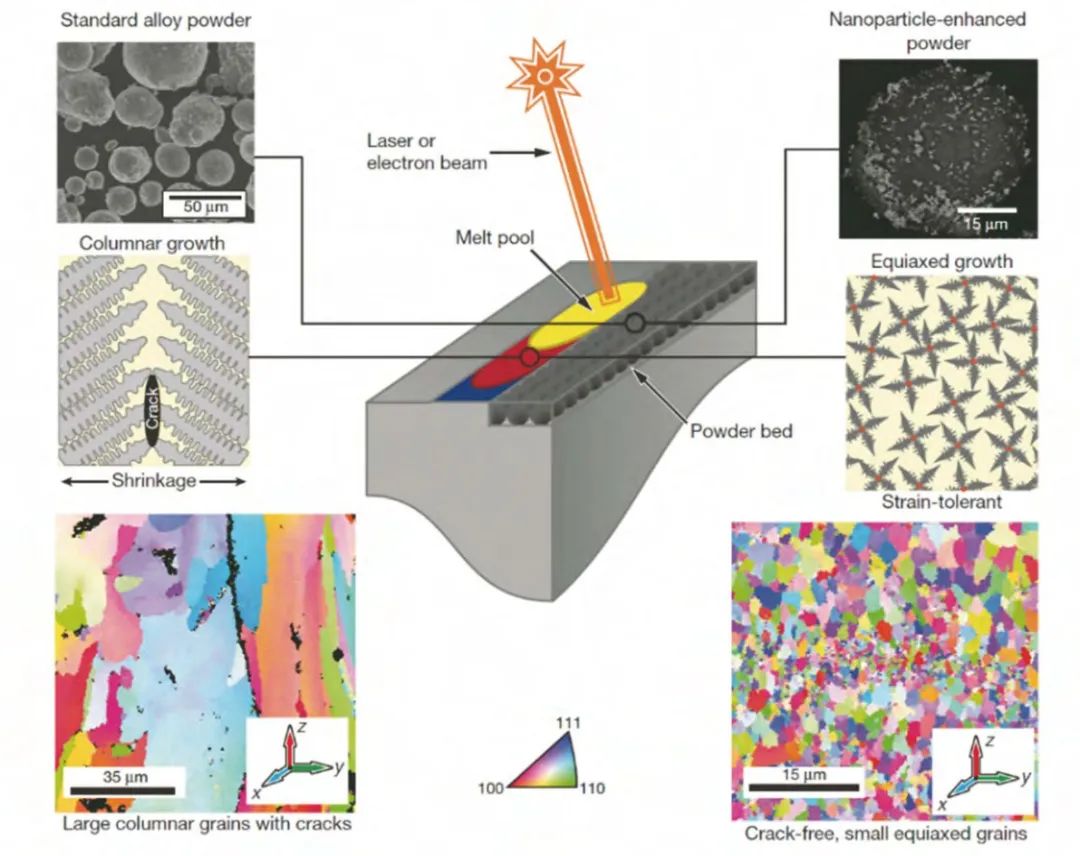
圖27075鋁合金的SLM增材制造:基于納米顆粒改性實現柱狀樹枝晶向微細等軸晶轉變及裂紋抑制
2.2激光增材制造鈦合金及鈦基復合材料
鈦基材料因具有優異的比強度、耐蝕性和生物相容性而被廣泛應用于航空航天、生物醫療、食品化工等領域,是激光增材制造經常采用的金屬材料。目前激光增材制造鈦基合金的挑戰在于:1)激光增材制造成形完全致密的復雜結構鈦基構件尚存在難度,成形過程中構件易產生氣孔、裂紋及表面球化等加工缺陷,這些加工缺陷往往會成為絕熱剪切帶和裂紋萌生源,降低成形件的力學性能和服役性能。2)激光增材制造過程中極大的冷卻速度(103~108K/S)和溫度梯度將誘發馬氏體相變,使構件內部產生較大的殘余應力;隨著加工層數增加,殘余應力逐漸增大,從而導致熱裂紋形成,并且成形件易發生翹曲,這種加工缺陷積累至一定程度時會導致成形件發生開裂,并嚴重降低零件的塑性和韌性。3)在激光加工過程中,熱流主要沿著平行于增材制造的方向傳導,導致體心立方(BCC)結構的初生β-Ti相沿散熱方向〈001〉β擇優生長,并具有很強的外延生長傾向,易形成粗大的柱狀晶組織,從而導致構件的顯微組織和力學性能具有很強的各向異性。
鈦基材料對SLM和LMD兩類激光增材制造工藝均表現出了較強的適用性。目前用于激光增材制造的鈦合金主要集中在工業純鈦(CP-Ti)及TC4等傳統鈦基材料上。激光增材制造構件的顯微組織調控是其力學性能提升的基礎,且與激光工藝參數密切相關?;赟LM工藝成形CP-Ti時,若采用較低的激光線能量密度,熔池熔體在凝固過程中會發生β-Ti向α-Ti的轉變,從而導致組織呈較為粗大的板條狀結構;隨著激光線能量密度增加,熔池凝固過程中較大的過冷度導致β-Ti向馬氏體α′-Ti發生轉變,此時成形組織呈顯著細化的針狀結構。SLM成形TC4構件的顯微組織通常為細小的針狀馬氏體。在增材制造方向上,初生β-Ti晶粒以柱狀晶外延生長,柱狀晶的長度可達100μm,遠大于SLM每層的鋪粉厚度(通常設為30μm);柱狀晶的寬度與熔道寬度相當,隨著激光能量密度的增加,熔道寬度增大,導致柱狀初生β-Ti晶粒粗化。Xu等學者發現,通過優化增材制造工藝參數,可將SLM過程中形成的脆性馬氏體相α′-Ti轉化成具有更高韌性的(α+β)-Ti組織,從而可以省去后續的熱處理。當增材制造層厚設為30μm時,熔池內部較大的溫度梯度及冷卻速度,使得凝固組織為馬氏體α′-Ti;隨著層厚增加至60μm或90μm,通過調控激光焦距可使α′-Ti發生分解,隨后轉變為細化的層狀(α+β)-Ti組織,有效提升SLM成形TC4構件的綜合力學性能。LMD成形的TC4構件通常表現出與SLM工藝成形構件相似的顯微組織特征,凝固組織為柱狀初生β-Ti晶粒。在凝固過程中,初生β-Ti晶粒沿增材制造方向穿過若干加工層發生外延生長,柱狀晶的長度通常為1.5~10mm,同時在初生β-Ti柱狀晶邊界上可觀察到α-Ti的晶界。通常情況下,LMD成形的TC4凝固組織不均勻:在靠近基板位置處,熔池的冷卻速度較大,會生成較細小的層片狀α-Ti組織及板條狀α′-Ti馬氏體組織;在構件頂部位置,冷卻速度較小,凝固組織為α+β層狀雙相組織;構件中部位置因受到持續的熱影響作用,鋁元素及釩元素易向α-Ti及β-Ti內部偏析,導致成形組織不均勻,且晶粒較粗大,易產生加工缺陷??梢?,激光增材制造雖涉及一系列復雜的工藝參數,但也為構件顯微組織與力學性能的設計和調控提供了可能。表2所示為不同激光增材制造工藝及后處理工藝條件下鈦合金的力學性能??梢姡す庠霾闹圃焘伜辖饦嫾牧W性能與顯微組織具有直接關系,而組織演變又受控于工藝,故高性能構件激光增材制造需要建立材料-組織-工藝-性能的一體化調控理論及方法。
表2激光增材制造鈦及鈦合金的力學性能
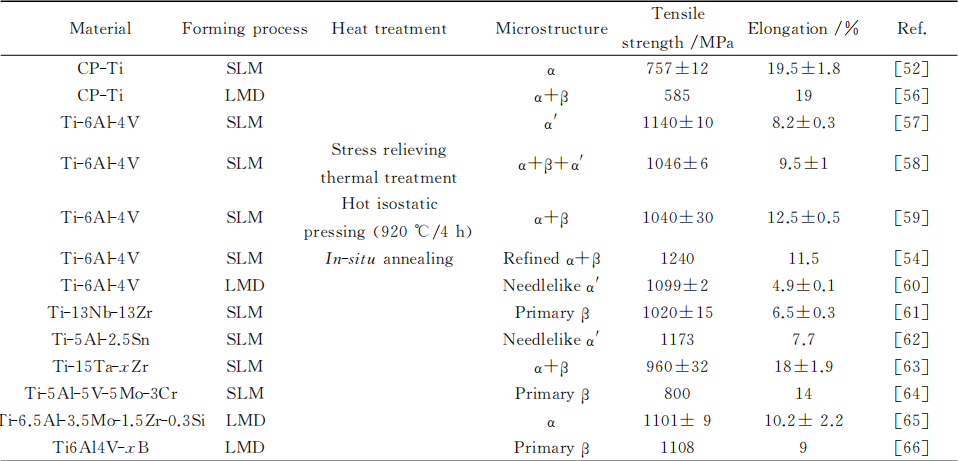
由于激光增材制造過程中熔池的冷卻速度較快,且沿著增材制造方向具有較大的溫度梯度,故而鈦合金的凝固組織往往呈柱狀晶結構,導致了成形件力學性能的各向異性。為改善鈦合金激光增材制造過程中產生的各向異性,可從材料設計和工藝優化兩方面加以改進。Nature報道了Zhang等學者研發的可用于激光增材制造的新型Ti-Cu合金,這類合金可在激光快速凝固過程中獲得細小等軸的初生β-Ti晶粒,如圖3(b)所示,且成形件內部沒有明顯的孔隙及裂紋,在增材制造方向上具有很高的化學成分均勻性。相比如圖3(a)所示的激光增材制造TC4的凝固組織,Ti-8.5Cu合金中的初生β-Ti晶粒得到了顯著細化,平均晶粒尺寸降至9.6μm。晶粒細化的主要原因是銅原子固溶在β-Ti基體中,顯著擴大了凝固過程中固液前沿的成分過冷區,且隨著銅在鈦中的含量增加,晶粒細化效應更加顯著。當銅的加入量為3.5%(質量分數)時,未經熱處理的成形樣具有較高的抗拉強度和延伸率,抗拉強度和延伸率分別為(867±8)Mpa和(14.9±1.9)%。NatureCommunicaTionS刊發了Barriobero-Vila等學者研發新型Ti-La合金的論文,該文闡明了α相穩定元素鑭對鈦合金相變過程及晶粒生長的作用機制。在鈦中加入質量分數為2%的鑭可使鈦合金在凝固過程中發生包晶、包析及共析反應(L1+β→La-bcc,La-bcc+β→α,La-bcc→La-fcc+α),同時在固/液前沿產生了較大的成分過冷,促進了細小等軸晶的形成。通過包晶反應形成的α-Ti與原始β-Ti不具有嚴格的取向關系,可使Ti-La合金構件的各向異性顯著降低。從激光增材制造金屬構件的顯微組織調控規律來看,晶粒的等軸化和均勻化有利于提升成形件的力學性能,而這也可通過在激光增材制造工藝中施加復合能場來實現。Qian研究小組通過在TC4構件LMD過程中復合20kHz的高頻超聲振動,使顯微組織從柱狀晶完全轉變為粒徑約為100μm的細小等軸晶,如圖4所示。在復合能場輔助下成形的TC4構件的屈服強度和抗拉強度均比直接采用LMD成形的構件提高了約12%,且這種基于復合能場改善顯微組織和力學性能的方法,對于Inconel625等鎳基高溫合金材料也同樣適用。
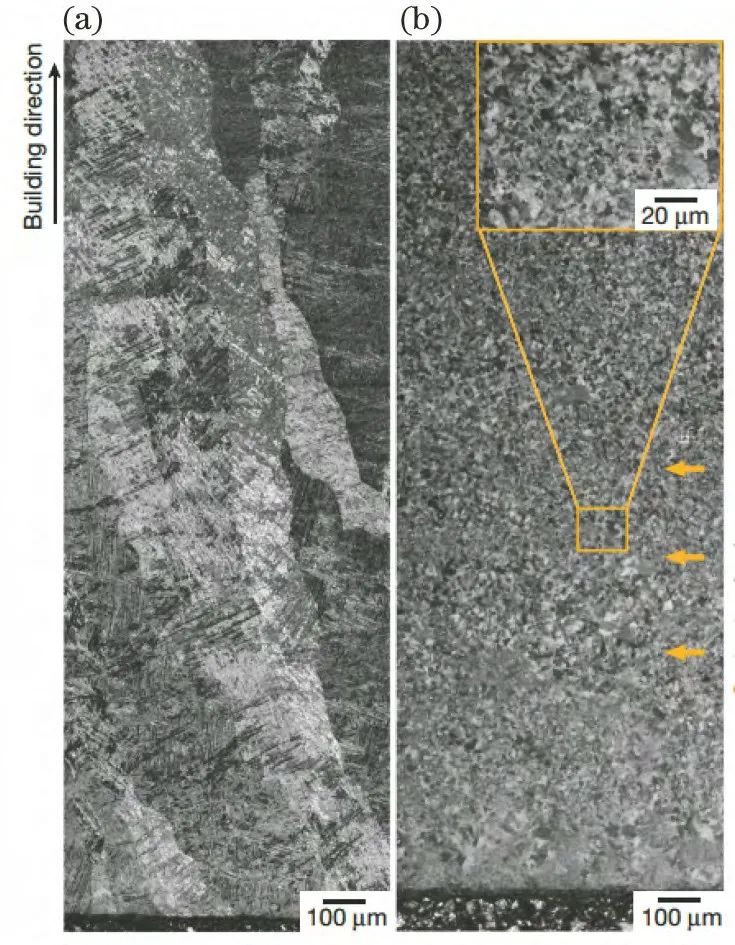
圖3激光增材制造TC4合金與Ti-8.5Cu合金顯微組織的對比。(a)TC4合金呈粗大的柱狀晶組織;(b)Ti-8.5Cu合金呈細小的完全等軸晶組織
除了上述基于合金化的思路來研發激光增材制造新型鈦合金外,制備陶瓷增強鈦基復合材料也是提升鈦基構件力學性能的重要手段。鈦具有很強的化學活性,激光增材制造過程中鈦組元易與其他組元發生原位化學反應,顯著增大了激光成形材料物相和組織的調控難度,故對于鈦基復合材料陶瓷增強相的選擇上需慎重。在眾多的陶瓷材料中,TiC及TiB2被認為是最適合用于鈦基復合材料的陶瓷增強相。它們具有與鈦合金相近的密度及熱膨脹系數,且具有較高的物理化學穩定性,可與鈦合金形成良好的物理化學兼容性。Liu等學者研究了LMD成形TiC-Ti6Al4V復合材料凝固組織與工藝參數之間的內在關系后發現:當激光功率為230W以及TiC陶瓷添加量為10%(體積分數)時,凝固組織中會出現初生球狀TiC、共晶TiC及共晶球狀TiC;隨著激光功率增大,凝固組織中開始出現細小的初生枝晶TiC;隨著激光功率進一步增至300W,這些初生枝晶長大,且數量增多。這種顯微組織演變的主要原因是TiC增強相在不同激光功率下的熔化程度不同。隨著激光功率增大,TiC增強相的熔化程度增大,更多的碳原子溶解在熔池中;當熔池中的碳原子含量增至一定程度時,初生枝晶TiC開始形成并附著在初生球狀TiC上。初生TiC的產生需要消耗一定的碳原子,導致凝固組織中共晶碳化物的含量降低。不同形態的TiC與鈦基體的結合能力不同,從而導致了不同的力學性能。當加入15%(體積分數)的TiC時,LMD成形TiC-Ti復合材料的抗壓

圖4超聲復合激光增材制造TC4合金的顯微組織調控。(a)激光熔化沉積復合高頻超聲振動工藝示意圖;(b)常規激光熔化沉積TC4合金的粗大柱狀晶組織;(c)超聲復合激光增材制造TC4合金的細小等軸晶組織
強度可達1450Mpa,斷裂應變超過13%。筆者研究團隊基于粉體完全熔化機制采用SLM工藝成形了納米TiC增強鈦基復合材料,研究后發現:TiC納米顆粒經激光熔化及凝固析出后,形成了均勻分布的納米層片狀增強結構,并可在較寬的激光線能量密度(0.25~1.0kJ/m)下保持這種新穎的納米增強結構,從而使激光增材制造構件具有優異的摩擦磨損性能(摩擦因數低至0.22,磨損率低至2.8×10-16m3·N-1·m-1);隨著激光能量密度進一步提高,層片狀納米TiC晶粒長大,甚至發生枝晶生長而失去納米結構,導致激光成形件的摩擦磨損性能顯著降低。Attar等學者研究了TiB2增強相對SLM成形鈦基復合材料顯微組織及力學性能的影響規律,發現:TiB2在SLM成形過程中完全溶解于熔池中,并在后續凝固過程中以納米級TiB的形式析出,形成新穎的Ti-TiB納米復合材料;同時,部分硼原子固溶在層片狀α-Ti中,起到了細化晶粒的作用;當加入體積分數為8.35%的TiB時,SLM成形TiB2-Ti復合材料的抗壓強度可達1636Mpa,斷裂應變超過17%??梢姡す庠霾闹圃焯赜械母吣芰枯斎?、瞬間高溫及超快熔化凝固過程,為鈦基復合材料增強體、基體的物相與組織調控提供了熱力學和動力學條件,并可使激光增材制造構件具有顯著區別于鑄造和粉末冶金等工藝制備的構件的顯微組織及力學性能。
2.3激光增材制造鎳基高溫合金及其復合材料
鎳基高溫合金自身含有較多的合金元素,其在激光增材制造過程中普遍存在裂紋敏感性強、元素偏析嚴重、顯微組織各向異性顯著、力學性能可控性差等問題。一方面,鎳基合金中親氧能力較強的鉻、鋁元素易在高溫作用下與成形氣氛中的氧元素發生作用,形成微細氧化物夾渣,然其與基體界面間的潤濕性較差,從而導致裂紋產生并降低力學性能;另一方面,碳、鈮、鉬等元素易在晶界聚集,顯著增加低熔點共晶相的含量,加劇了熱影響區熱裂紋的形成。此外,各類晶界析出物會消耗鎳基體中的強化相形成元素,顯著降低激光增材制造鎳基構件的力學性能。當前,鎳基高溫合金激光增材制造主要集中在Inconel系列合金上,其中沉淀強化型Inconel718和固溶強化型Inconel625的可焊接性強,亦適用于基于粉末熔化/凝固冶金過程的激光增材制造工藝。激光增材制造Inconel系列合金的組織在成形方向上為明顯的柱狀晶,具有較強的成形方向〈001〉織構,而在水平方向則呈胞狀組織;而且,合金易在晶界析出碳化物、LaveS等脆性相。因此,激光增材制造鎳基高溫合金的顯微組織調控主要是通過優化工藝參數進而改變熔池的溫度梯度、凝固速度和冷卻速率來實現的,然后結合后續的熱處理工藝來實現晶粒形狀、尺寸以及析出相形態、含量及分布的調控。此外,采用優化的激光掃描策略也可改變晶粒的生長織構,獲得高強韌鎳基合金材料。激光增材制造鎳基高溫合金工藝優化機制的相關研究表明:高的掃描速度和低的激光功率會導致較低的激光能量輸入,故熔池熔體的黏度及潤濕性較差,未熔顆粒及不規則孔隙較多,成形件表面球化缺陷也較嚴重;隨著掃描速度減小及激光功率增大,熔體的流動性及潤濕性提高,熔體鋪展均勻,成形質量提升;過高的激光能量密度會增大熔體的不穩定性,易產生氣孔及裂紋等缺陷,影響構件的力學性能。Wan等學者研究了激光掃描策略對Inconel718晶粒形態及織構的影響規律,發現掃描策略可以改變熱流及晶粒的生長方向:進行單一線性掃描時,層與層間的熱流方向相似,易形成定向柱狀組織;而在層間旋轉90°掃描時,熱流方向不斷旋轉,晶粒生長競爭機制顯著加強,可以獲得較強的立方織構。熱處理可在一定程度溶解拓撲密排相(δ相、σ相等)及碳化物等析出相,提高γ′及γ″強化相的含量,提升材料的力學性能。Zhang等學者發現SLM成形Inconel625經均勻化熱處理可有效減少元素偏析,消除δ相,使組織更均勻。Sui等學者針對LMD成形Inconel718的熱處理工藝進行優化后發現:在1050℃保溫15min可以使LaveS相由不規則的長條狀轉變為細小的顆粒狀,且隨著保溫時間延長,LaveS含量增多;長條狀LaveS相易成為裂紋源,同時會使強化相γ″分布不均勻,而細小的顆粒可隨基體一起變形,并起到強化作用,使試件的抗拉強度達到1341Mpa,延伸率達到19.1%。此外,基于高溫高壓處理的熱等靜壓(HIP)技術可以消除激光增材制造鎳基高溫合金構件中的殘余孔隙,抑制裂紋萌生及擴展,進而提高成形件的力學性能。由表3可知:熱處理可實現激光增材制造鎳基高溫合金的強化,但會在一定程度上犧牲材料的韌性;同時,后處理需要合理調控加熱溫度、保溫時間、冷卻介質及熱等靜壓的壓力等參數,成本較高,工藝較復雜,缺陷形成概率也較大。
表3激光增材制造鎳基高溫合金及其復合材料的力學性能
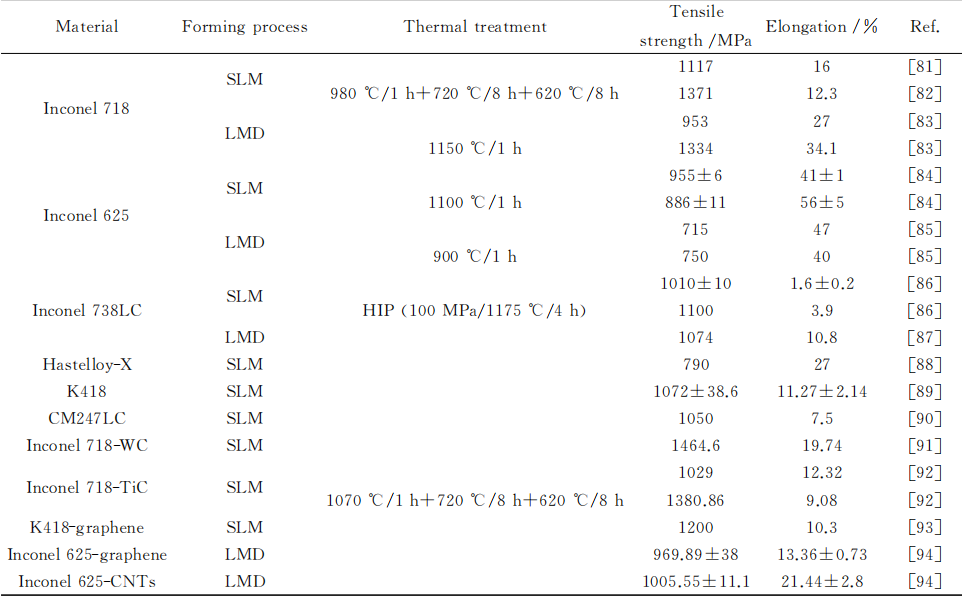
制備陶瓷增強鎳基復合材料是鎳基高溫合金力學性能提升的另一個重要途徑,可使復合材料在韌性不降低的前提下具有更高的比強度、比剛度及耐熱性。Ma等學者制備了Ni/Al2O3納米復合材料,發現添加納米顆粒后可顯著減小復合體系的熱影響區而增大熔化區,如圖5所示,揭示了激光作用下鎳基納米復合材料特殊的熔化、凝固特性。此反?,F象主要是由于納米顆粒會減小體系的熱導率,進而降低對基板的傳熱;同時,納米顆??稍龃笕垠w的黏度、抑制熱毛細流動,進而減少熔池的熱對流。筆者研究團隊針對WC、TiC等微米陶瓷顆粒增強鎳基(Inconel718、Inconel625等)復合材料體系,基于SLM和LMD兩類激光增材制造工藝,通過激光工藝參數和復合材料組分調控,在陶瓷增強顆粒與γ基體間構建了(Ti,M)C(M為Nb、Mo)梯度界面層,有效控制并消除了界面殘余應力、界面微孔及微裂紋等成形缺陷,如圖6(a)所示,并揭示了激光作用下梯度界面的形成機制、顯微結構特征、界面結合性能;此外,筆者研究團隊還發現梯度界面可以有效改善陶瓷/基體界面的潤濕行為,平衡兩者的硬度差異,并可起到傳遞載荷、調節增強顆粒與基體變形行為的作用。筆者研究團隊構建了基于增強相/基體間梯度界面設計與調控實現顆粒增強鎳基復合材料構件強度和韌性協同提升的調控原理,解決了激光增材制造復合材料構件通常面臨的強度升高、韌性降低這一對“強”與“韌”的矛盾。
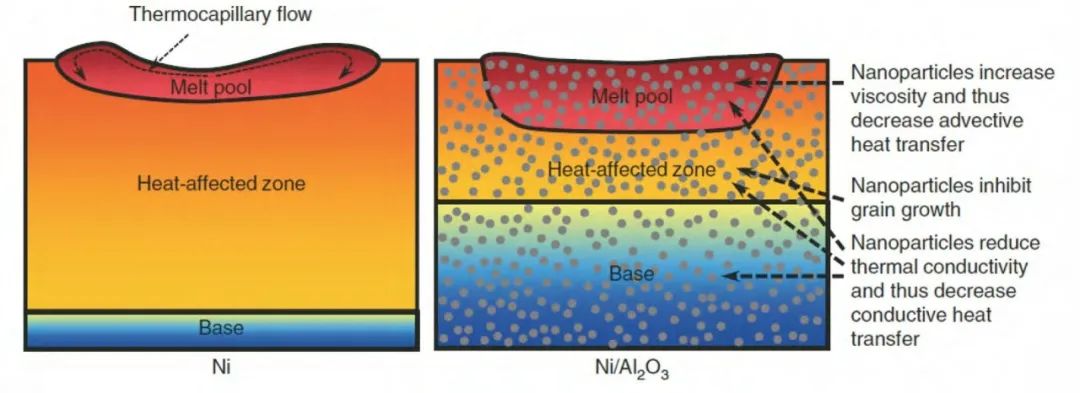
圖5激光熔化鎳基復合材料納米粒子的冶金改性機制
這種在陶瓷增強顆粒與金屬基體之間構建梯度界面層的工藝調控思路,在WC、TiC增強鐵基復合材料激光增材制造工藝調控中也具有普適性和可行性;同時在以傳統微米陶瓷顆粒為增強相的條件下,為抑制復合材料界面缺陷、提升界面結合性能及構件成形性能提供了有益的思路。Ho等學者也發現在激光增材制造WC-W2C/Inconel718復合材料中晶粒易在WC-W2C表面形核,并在界面形成擴散層,該顯微組織演變源于增強相與基體之間較小的潤濕角及半共格界面。另一方面,筆者團隊研究后發現,納米TiC陶瓷顆粒增強鎳基復合材料的激光增材制造,可減小柱狀晶及裂紋形成的概率,基體組織為胞狀晶且增強相分布均勻,如圖6(b)所示。這是由于納米增強顆粒易成為基體熔體的非均勻形核點,從而提高基體的形核率,促進胞狀晶形成并細化組織。基于納米陶瓷復合及納米改性的思路,通過激光增材制造非平衡快速熔化凝固過程中冶金熱力學和動力學行為的理解與調控,可實現對納米顆??臻g分布、晶體生長組織和形態的調控與布局,以此亦可實現激光增材制造鎳基復合材料構件強度和韌性的協同提升。此外需要指出的是,當前激光增材制造復合材料構件的多功能化也是增材制造技術的一個重要研究方向,筆者通過調控激光工藝參數實現了鎳基納米復合材料表面粗糙度的調控,獲得了超疏水表面,并使鎳基復合材料具有優異的耐蝕性,如圖6(c)所示。
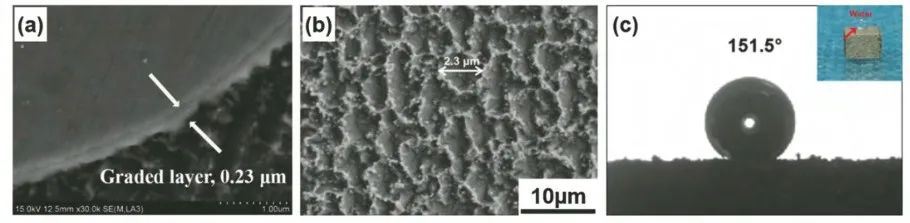
圖6激光增材制造鎳基梯度界面復合材料和納米復合材料的組織與性能調控。(a)微米WC增強復合材料的梯度界面;(b)納米TiC增強復合材料的胞狀組織;(c)鎳基納米復合材料的超疏水表面
3、航空航天典型結構的激光增材制造
3.1大型金屬構件的激光增材制造
應用于航空、航天、船舶、核電等現代工業的大型金屬構件正朝著復雜化、一體化、高性能化方向發展,LMD技術已證實可滿足大型金屬構件的成形要求。LMD工藝若要在鈦合金、鎳基高溫合金、高強鋼、難熔合金等難加工金屬材料大型關鍵構件上獲得更廣泛的工業應用,仍需進一步解決兩大關鍵難題:一,高能激光長時間劇烈非穩態循環加熱和高速冷卻條件下,成形材料的晶粒形態及顯微組織很難控制,以凝固晶粒、內部缺陷及顯微組織為核心的冶金質量和性能控制是激光增材制造大型金屬構件的基礎難題;二,激光增材制造過程中熱應力、組織應力、凝固收縮應力等多種類型復雜應力的累加與耦合,易導致大型金屬構件變形,甚至開裂,大大制約了大型金屬構件激光增材制造的控形與控性。
Todd研究小組在NatureMateriAlS上發文指出,增材制造技術實現工業應用的最大障礙是成形件中的熱應力及多種結構缺陷。北京航空航天大學王華明院士認為,內應力及變形開裂是長期制約金屬構件激光增材制造技術發展的瓶頸。鈦合金密度低、比強度高、耐蝕性強,已被廣泛應用于飛機發動機構件、主承力構件、起落架等,但其較差的加工性能制約了它的工程應用范圍。北京航空航天大學王華明院士團隊突破了飛機鈦合金大型主承力構件激光熔化沉積增材制造的關鍵工藝技術,研制出了國際領先的飛機鈦合金大型結構件激光增材制造工程化成套裝備,該設備的成形室尺寸為4000mm×3000mm×2000mm。此外,該團隊還實現了TA15、TC4、TC11等大型復雜整體結構主承力飛機鈦合金加強框及A-100超高強度鋼飛機起落架等關鍵構件的激光增材制造,實現了激光增材制造主承力構件的裝機應用,如圖7(a)所示。該團隊還提出了大型金屬構件LMD成形過程“內應力離散控制”新方法,形成了大型結構件內部缺陷、質量控制及其無損檢驗的關鍵技術,成形的飛機鈦合金構件的綜合力學性能達到或超過了模鍛件。該團隊建立了金屬構件激光增材制造過程中凝固晶粒形態主動控制理論,實現了具有梯度組織和梯度性能的先進航空發動機鈦合金整體葉盤及大型關鍵主承力構件的制造,如圖7(b)所示。該團隊制造的航空發動機鈦合金葉片為定向生長的全柱狀晶組織,具有優異的高溫持久蠕變性能,輪盤為等軸晶凝固組織,具有優異的各向同性力學性能,如圖7(c)所示。
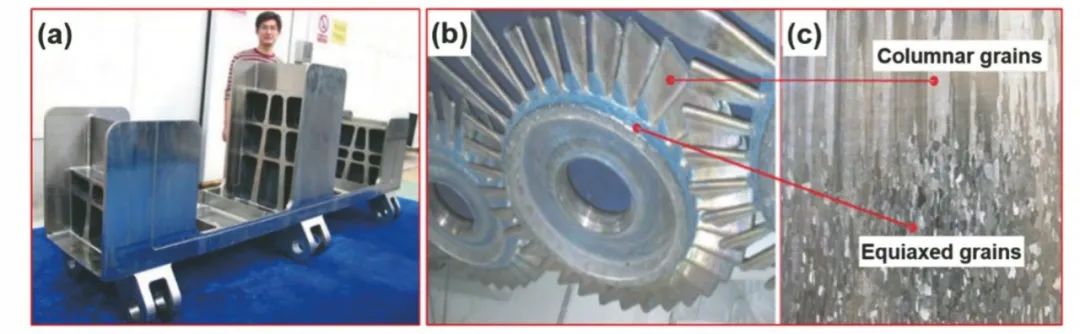
圖片圖7大型整體金屬構件的激光熔化沉積LMD增材制造。(a)鈦合金飛機大型關鍵主承力構件;(b)航空發動機梯度性能鈦合金整體葉盤;(c)輪盤-葉片梯度過渡區的凝固晶粒組織
西北工業大學黃衛東、林鑫教授團隊面向中國C919中型客機的需求,利用LMD增材制造技術制造了TC4合金體系C919飛機翼肋緣條,其長為3100mm,如圖8(a)所示,探傷和力學性能測試結果皆符合中國商飛的設計要求。在構件力學性能的考核中,LMD增材制造TC4合金試件的高周疲勞性能優于實測鍛件,且抗拉強度和屈服強度的批次穩定性優于3%。近年來,隨著高功率激光器、高速掃描振鏡等硬件的不斷升級,SLM裝備的研制水平持續提高,該團隊研制的SLM裝備成形尺寸可達600mm×600mm×600mm。采用四激光器、四振鏡協同可以提升增材制造的效率,相比單激光、單振鏡加工效率可提升100%~200%。大型SLM裝備的發展為結構更為復雜的大型整體金屬構件的成形開辟了新途徑,該團隊基于SLM成形的鈦合金風扇葉片包邊長度可達1200mm,具有復雜的空間曲面結構,且成形尺寸精度較高,如圖8(b)所示;基于SLM成形的鎳基高溫合金發動機機匣尺寸達到了Ф576mm×200mm,為發動機關鍵零部件的設計、制造及應用驗證提供了重要的技術支撐。
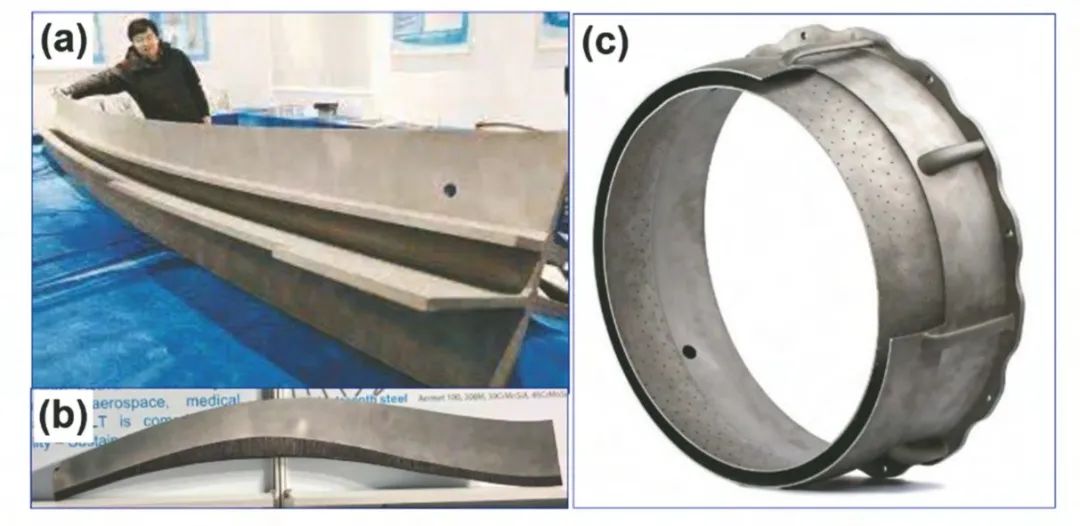
圖8大型復雜金屬構件的LMD及SLM增材制造。(a)LMD成形C919鈦合金翼肋緣條,長為3100mm;(b)SLM成形鈦合金風扇葉片包邊,長為1200mm;(c)SLM成形鎳基高溫合金發動機機匣,尺寸為Ф576mm×200mm
3.2復雜整體結構的SLM
隨著航空航天領域對熱端部件服役性能要求的日益提高,整體結構的設計與制造越來越受到重視,其內含復雜內流道結構、多孔點陣結構等難加工結構,已超出傳統工藝的成形制造能力,而基于SLM高精度增材制造技術可使這些復雜整體結構的快速制造成為可能。近年來,航空航天領域采用SLM技術成形的典型整體構件包括火箭推進器耐高溫部件、發動機燃油噴嘴、燃燒室導流襯套等。美國國家航空航天局(NASA)和AerojetRocketdyne公司合作,基于SLM增材制造技術實現了液氧、氣態氫火箭助推器的整體制造。助推器是火箭發動機系統的重要組成部分,在制造成本中占最大部分。NASA和AerojetRocketdyne公司在嚴格的測試環境中對激光增材制造的助推器整體結構開展了點火試驗,如圖9(a)所示,實現了結構減重、制造效率和服役性能的顯著提升。整體結構的增材制造技術已證實對未來的空間探索至關重要。借助于激光增材制造技術,NASA提出了火箭發動機核心部件“制造速度提升10倍、生產成本降低50%以上”的目標,其基于SLM技術成形的如圖9(b)所示的火箭發動機燃燒室銅襯套整體構件是其近年來的成功實踐。該整體構件面向的是導電、導熱性很強的銅合金,該合金是典型的激光增材制造難加工材料。該整體構件是基于GRCo-84銅合金采用SLM工藝,經258h、8255層增材制造而成的。火箭發動機燃燒室內推進劑的燃燒溫度超過了2760℃,故在銅合金襯套內部一體化成形了200多個隨形冷卻流道,溫度在-173℃以下的氫在流道中循環冷卻,以防止構件在服役過程中發生熔化。對于襯套整體構件內部幾何形狀復雜的微細流道,其結構優化設計及激光增材制造成形質量,將直接決定發動機燃燒室的冷卻效率及其服役性能和壽命。對于輕量化薄壁構件內部的一體化隨形冷卻流道,其延伸和布局路徑受整體結構形狀的約束,同時流道的尺寸和結構也制約著整體構件的激光成形性,故而向增材制造技術的發展提出了更大挑戰及更高要求。
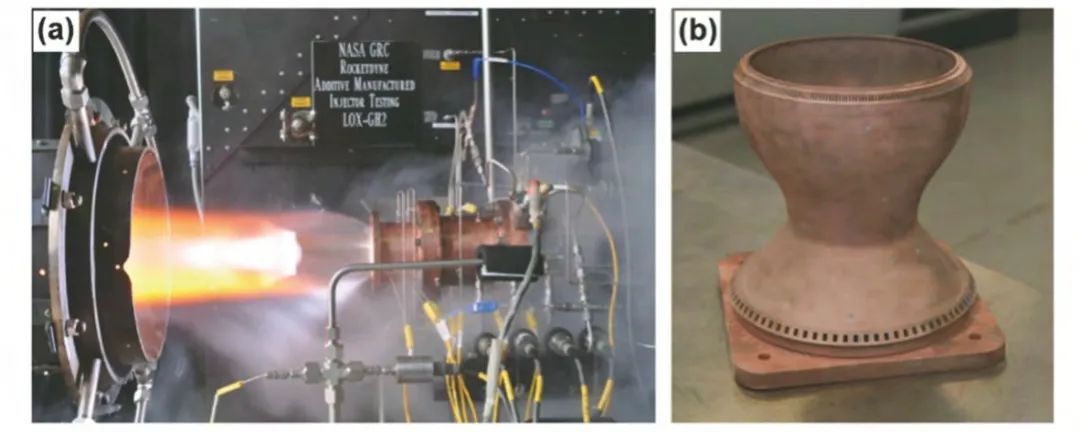
圖9NASA基于SLM成形的銅合金整體構件及性能測試。(a)NASA和AerojetRocketdyne公司開展的激光增材制造構件點火試驗;(b)火箭發動機燃燒室銅合金襯套整體構件
美國通用電氣(GE)公司基于SLM增材制造技術研發了先進渦槳發動機(ATP)內部新型燃油噴嘴,如圖10所示,這是近年來復雜整體結構增材制造航空工業應用的典型案例。燃油噴嘴一般位于發動機燃燒室之前,其主要作用是提供燃料的輸送。在發動機運行過程中,空氣經各級葉片的壓縮之后被輸送到發動機燃燒室內,與此同時燃料通過燃油噴嘴霧化或氣化并被輸送到燃燒室內,點火后燃料在燃燒室中充分燃燒,進而實現發動機的持續運轉。因此,燃油噴嘴對加速混合氣體形成,保證燃料穩定燃燒和提高燃燒效率具有重要作用。燃油噴嘴作為典型的復雜裝配體,無論是成形制造還是裝配組裝,工序多,工裝多,耗時長,成本高,且加工精度及穩定性很難達到使用要求,對于傳統制造技術來說都是一大挑戰。針對這一難題,GE公司采用SLM技術加工Inconel718鎳基高溫合金,實現了燃油噴嘴的整體設計與制造,將原先20個小部件的“組件”變成一個整體化燃油噴嘴構件,如圖10(c)所示。這不僅可以消除不同部件之間冗余的連接結構,還可對燃油噴嘴結構進行優化設計,從而在從高到低的較寬燃油流量下實現良好的霧化效果,并抑制燃油霧化不充分的問題,進而減少積碳。GE公司基于增材制造技術整體設計制造的這款燃油噴嘴實現了25%的減重效果,同時縮短了制造周期,降低了生產成本,且增材制造燃油噴嘴的使用壽命提升了5倍以上。目前,GE公司這款燃油噴嘴的生產能力為每年35000~40000件,已應用在空客A320neo、波音737MAX、商飛C919和波音777-8等機型上。
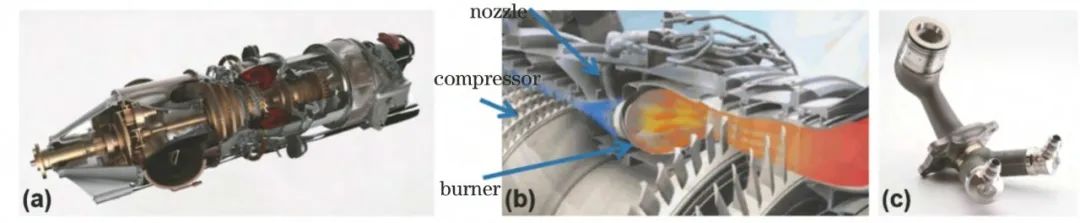
圖10GE公司基于SLM技術制造的航空發動機燃油噴嘴構件[110]。(a)先進渦槳發動機(ATP);(b)燃油噴嘴在發動機內的工作原理;(c)激光增材制造燃油噴嘴構件
3.3輕量化點陣結構的SLM
對于航空航天飛行器而言,減重是永恒不變的主題,而傳統制造方法已將零件減重的可能性發揮到了極致。將點陣結構優化設計與增材制造技術相結合,可使構件具有高比強度和高比剛度等優異的力學特性。激光增材制造技術因具有疊層自由制造的工藝特性,賦予了復雜輕量化結構極高的設計及成形自由度,可成形傳統加工方法難以成形的輕量化復雜點陣結構。近年來,激光增材制造成形復雜構型輕量化點陣結構已成為熱點研究方向之一,可為航空航天等領域輕量化金屬構件性能及功能的突破帶來新契機。Tancogne-dejean等美國學者將經典八隅體桁架結構應用于激光增材制造點陣結構中,設計出了在動態和靜態載荷下均具有優異的能量吸收功能的八隅體金屬點陣結構,成形結構在應變速率高達103S-1條件下仍具有良好吸能效果。除了將傳統經典結構應用于激光增材制造點陣結構設計外,基于自然啟迪的創新點陣結構設計也為構件性能帶來了突破。Pham等英國學者基于金屬晶體硬化機制,借鑒金屬晶格微尺度結構及位錯、晶界等多種強化機理,設計了一種仿晶格點陣結構,該結構相對于傳統規則的點陣結構具有更加優異的耐損傷特性,如圖11所示。此外,基于拓撲優化的點陣結構設計正成為金屬構件輕量化及強韌化的重要途徑之一。PaneSar等英國學者詳盡闡述了拓撲優化技術在激光增材制造點陣結構設計方面的策略及應用,并發現經拓撲優化后的點陣結構的比剛度較傳統規則的點陣結構至少提高了40%~50%。可見,增材制造技術在航空航天點陣結構產品設計與制造領域已展現出一定的發展與應用潛力,并以輕量化和高性能作為主要考核目標。
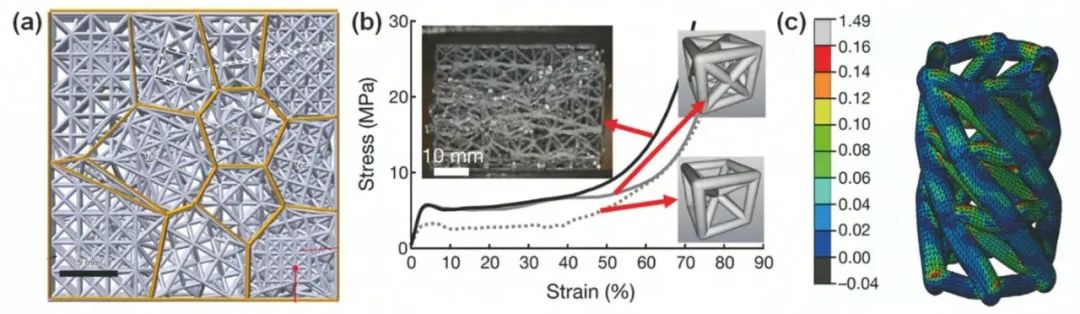
圖11基于金屬晶體硬化機制設計的仿晶格點陣結構的增材制造。(a)仿金屬微晶格點陣結構;(b)單相與多相晶體點陣結構的應力應變差異;(c)數值模擬得到的仿密排六方晶體點陣結構(HCP)的應力分布
激光增材制造點陣構件已在國際民航客機制造領域獲得了實際工程應用,空客商業飛機機艙隔板是近年來的成功案例。該結構主要用于隔離機艙乘客區與乘務員區域,同時還兼具應急擔架和機組人員安全座椅的功能,如圖12(a)所示,故要求該構件在保證強度的同時盡可能減重。空客公司基于SLM技術設計和制造了仿生點陣結構機艙隔板,如圖12(b)所示。在成形材料上,此隔板構件選用新型輕質高強鋁合金ScAlmaolly[115-116],該合金為稀土元素鈧微合金化Al-Mg合金,具有較低的密度(2.67g/cm3)和良好的SLM加工工藝性能。鈧元素可顯著細化鋁合金晶粒,故SLM成形合金構件具有優良的力學性能(抗拉強度約為520Mpa,延伸率約為13%),可作為未來輕量化結構件及點陣構件的理想材料。在結構設計上,空客研發人員基于生物啟迪實現了跨尺度仿生點陣結構設計,如圖12(c)所示,在宏觀尺度上基于“黏菌自適應網絡”算法實現了主體結構設計,該算法以最小的行數連接一組點并使每個點至少與兩條線相連,因此在一條線出現失效時該點仍連接在整個設計結構中,可保障整體構件的結構完整性和結構強度。在微觀尺度上,該構件借鑒了骨骼生長的生物靈感,完成了超過66000個網格的排布,實現了微觀網格稠密度與應力分布相匹配,最終使得跨尺度仿生點陣構件較原蜂窩復合材料隔板結構在相同沖力下(9g重力加速度)的位移減少了8%(9mm)。在成形工藝上,該構件采用SLM技術實現復雜零部件一體化高效成形,如圖12(d)所示,最終的機艙隔板構件由112個部件組裝而成,相較于原蜂窩復合材料隔板構件減重45%(30kg),從而可使空客每年節省465000t二氧化碳排放量,并有望批量化應用于A320客機上。
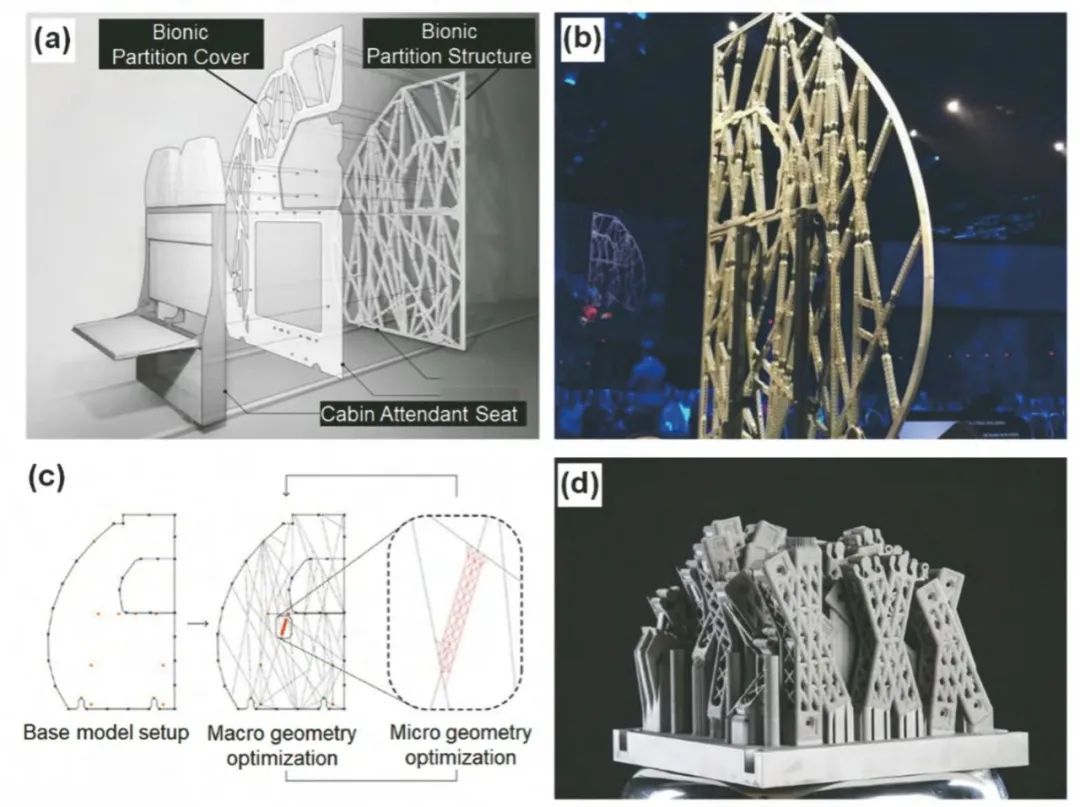
圖12空客公司基于SLM技術設計制造的新型仿生點陣結構機艙隔板。(a)機艙仿生隔板結構圖;(b)機艙仿生隔板實物圖;(c)跨尺度仿生結構設計;(d)機艙仿生隔板零部件選區激光熔化成形實物圖
3.4多功能仿生結構的SLM
激光增材制造金屬構件正從高性能化向多功能化發展,Nature以“推開3D打印的限制”為題發表評述指出,材料和結構的創造將助力3D打印技術的發展,并建議“向自然界‘借’材料、‘借’結構”,道法自然,突出生物仿生(biomimicry)、生物靈感(bio-inSpired),以實現預期的功能。未來增材制造的發展將更加凸顯材料的創造、結構的仿生以及多功能的集成優化。生物系統經過數十億年的進化和自然選擇,已形成并優化了其復雜的多層級組織結構,以達到最優的性能/功能來應對環境的變化。許多生物系統具有獨特的多功能組合,而這往往是人工合成材料難以實現的?,F代分析表征技術已證實,天然材料的優異性能或特殊功能,是依靠其內部復雜的多層次結構實現的,其尺度范圍通常橫跨納米尺度到宏觀尺度。對于性能/功能驅動的增材制造,基于生物靈感的仿生結構設計,是創新增材制造結構的重要途徑之一,并有望實現增材制造結構性能/功能的躍升。
Nature刊發的題為《生物材料進化的啟迪及其應用》綜述性論文認為,生物材料蘊含著大量的源自于自然界的成分與結構信息,并指出盡管生物材料的化學成分一直是其設計關注的焦點,但對于其在非醫學領域的潛在應用,應更關注其在結構拓撲優化、力學性能、功能等方面的物理屬性及響應。Sciencs以《賦予遠古材料新的機會》為題刊發綜述性論文,該文指出,蜘蛛網所具有的高強度和高延展性的優異組合是迄今為止人工合成材料無法獲取的;從材料本質上而言,蜘蛛絲實際上是一種相對簡單的蛋白質,但生物結構賦予其高性能及多功能。這種基于生物啟迪的結構設計與仿生優化,有望用于構建多功能的材料及構件系統。仿生的本質是學習天然結構的設計方法及材料布局,這是一個從納/微觀尺度向宏觀尺度連續演變的大跨尺度結構設計。AdvancedMateriAlS刊發的綜述性論文《仿生材料微/納米制造:自然結構仿生的方法綜述》”給出了仿生結構設計的一般性方法,其程序包括:基于預期獲取的獨特功能在生物系統中尋找生物靈感;建立跨尺度仿生結構與宏觀性能/功能之間的關系;設計遴選合適的材料及工藝;構建仿生結構以實現所需的功能。同時,該論文指出仿生設計在原理上很簡單,但在實際制造中卻有相當難度,原因主要是多材料合理匹配與布局的挑戰及微/宏大跨尺度仿生結構制造工藝的約束性。
筆者研究團隊基于下一代高超音速飛行器、空間探測器等航空航天裝備的整體化、多功能化發展趨勢及潛在工程應用,面向減振抗沖擊、隔熱/防熱等綜合功能需求,創新發展了仿生結構及材料布局,實現了仿生結構的激光整體增材制造及其多功能化,其中涉及結構、材料、工藝、功能等多因素的耦合、匹配及一體化調控。面向減振抗沖擊功能,一是考慮口足目生物口蝦蛄(別稱皮皮蝦)尾節,如圖13(a)所示,其獨特的生物結構能使其抵抗競爭捕食過程中超過1500N、23m/S的沖擊力,其能量吸收機理類似于沙袋,本身吸收和消散能量,而不使能量反向傳遞。通過解析皮皮蝦尾部的宏觀構型,筆者團隊設計了一種仿生雙向波紋板結構,揭示了高度和波長兩個結構變量對仿生結構在沖擊載荷作用下的比能量吸收(SEA)、沖擊力效率(CFE)及應力分布的影響規律,該結構的SEA可達到45J/g,CFE最高為85%,這表明其具有優良的能量吸收能力及抗沖擊穩定性。二是考慮水蜘蛛在水下構建的住所———潛水鐘,如圖13(d)所示,其能長時間承受不同流速、不同方位水流的沖擊,具有優異的韌性和抗沖擊能力,并具有桁架結構和薄殼結構的輕量化特征。針對仿生水蜘蛛潛水鐘網殼結構尺寸跨度大、懸垂結構多、加工難度大等難題,筆者團隊研究了網殼結構基本結構單元特征對SLM成形構件尺寸精度、致密化行為和壓縮性能的影響規律,揭示了仿生網殼構件在壓縮過程中的變形行為及斷裂機制,并發現隨著網殼支柱直徑增加,主導斷裂機制從應力控制斷裂轉變為孔隙率控制斷裂。三是考慮到黃道蟹蟹鉗具有密集螺旋排布的多孔道結構特征,筆者團隊通過建立參數化仿生結構三維模型,基于SLM工藝研究了旋轉增量和孔道分布特征對仿生蟹鉗結構變形行為的影響規律;結果發現,SLM成形件截面熔池堆疊方式呈顯著的螺旋特征,較小的旋轉增量易導致試件在壓縮過程中發生扭轉破壞/失效,并發現基于仿生設計引入的孔道結構因在壓縮變形過程中發生彈性屈曲而顯著提高了SLM成形件的韌性。針對隔熱/防熱功能,考慮到挪威雪杉能在極寒環境下生存并能抵御強風的特點,筆者團隊以其莖干截面顯微結構為設計靈感,構建了一種兼具承載及隔熱/防熱功能的可重復使用的熱防護結構,建立了以梯度分布的中空管為功能層并配合兩個面板層形成夾層的熱防護結構,該結構的熱導率僅為2.321W/(m·K),比壓縮強度高達98.99Mpa/(g/cm3),仿挪威雪杉熱防護結構可兼具良好的力學性能和熱防護性??梢姡律O計為功能驅動的增材制造結構優化及多功能化提供了新途徑,但“結構易仿、制造不易、科學更難”,其中涉及的關鍵科學難題包括:仿生微結構與構件典型功能的映射關系及優化模型;仿生設計的跨尺度結構激光增材制造工藝約束性及成形機制;激光增材制造仿生結構的多功能一體化評價方法及響應機制等。因此,增材制造新技術與仿生結構設計相輔相成、相得益彰,而關鍵科學問題的研究則貫穿于材料-結構-功能一體化的全過程各領域。
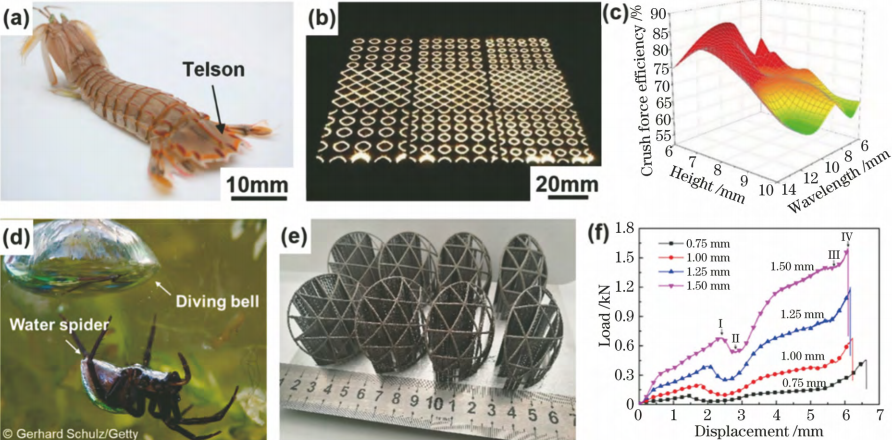
圖13激光增材制造輕量化抗沖擊仿生功能結構。(a)皮皮蝦尾節宏觀形貌;(b)仿生雙向波紋板抗沖擊結構SLM加工;(c)仿生雙向波紋板結構高度和波長參數對沖擊力效率(CFE)的影響;(d)水蜘蛛及其在水下構建的住所———潛水鐘;(e)SLM成形仿生網殼結構;(f)仿生網殼結構的壓縮力-位移曲線
4、結束語
增材制造具有豐富的科學內涵,主要體現在:1)圍繞“增”字,涉及“工藝調控基礎”,激光增材制造涉及高能激光與金屬粉體的作用機理及復雜構件逐層堆積工藝的調控機制,特別是對于激光與粉末物質的作用,其尺度是幾十至數百微米的顆粒量級,是一個典型的介于微觀和宏觀之間的“介觀”尺度問題;2)圍繞“材”字,涉及“材料設計基礎”,主要涉及激光增材制造金屬、合金及金屬基復合材料的設計、制備方法及成形機制,其中激光成形材料顯微組織調控是典型的“微觀”尺度問題;3)圍繞“制造”一詞,則涉及“結構與性能/功能基礎”,尤其是增材制造構件結構優化及性能/功能調控,是典型的“宏觀”尺度問題??梢姡す庠霾闹圃旒夹g的發展趨勢是實現微觀-介觀-宏觀跨尺度的材料-結構-工藝-性能/功能一體化,這是由其科學內涵所決定的。思考激光增材制造技術未來的研究與發展趨勢,下列方向值得進一步關注:
1)以高性能/多功能為驅動的激光增材制造材料-結構-工藝一體化及性能/功能的主動實現。傳統的材料-結構-性能/功能一體化的思路,是在選材的基礎上,通過結構設計和加工工藝來獲取一定的性能/功能;在這種“自上而下”的方法中,性能/功能的實現是被動的,也存在反復試湊與優化的過程。而未來激光增材制造技術的發展則可從擬實現的性能/功能出發來主動選擇材料,并強調設計的廣義性(除了結構設計,材料、工藝甚至性能/功能本身都需要設計)及增材制造工藝的可控性(達到高速、高效、高精度、高可靠性的效果),進而主動實現預期功能。特別是在航空航天領域機械系統復雜度不斷提高、構件性能/功能集合度不斷增強的發展趨勢下,采用這種性能/功能驅動的“自下而上”的材料-結構-工藝一體化的思路,對于在復雜加工系統中主動實現增材制造構件的高性能和多功能化具有重要意義。
2)面向激光增材制造的“多相材料”和“多材料”設計、制備與成形,以實現將“合適的材料添加到合適的位置”。面向激光增材制造的新型二元或多元合金、納米顆粒改性金屬基復合材料、原位增強金屬基復合材料等“多相材料”(mulTiphaSemateriAl)的設計與制備,是解決傳統金屬材料比強度和比剛度低、耐蝕性差等劣勢的有效途徑,而激光成形材料本身仍是均質材料。一方面,多相材料的精準設計可以通過材料設計軟件和高通量實驗方法加以定制,定量預測材料成分和組元對激光加工性能和增材制造構件性能的影響規律,目標是在短時間內篩選出具有預期特性及性能的多相材料,以提高激光增材制造新材料的研發成效。另一方面,隨著強化相粒子(如陶瓷顆粒、稀土元素及原位形成的化合物等)相繼被引入到激光增材制造高性能金屬構件中,強化相的形成機制、分散狀態及界面結合性能等問題制約著增材制造構件的高性能化,故可采用原位分析技術(如高速同步輻射X射線顯微成像技術、中子小角散射實驗技術等)研究強化相的運動與分布行為、冶金缺陷形成規律及顯微組織演變規律,這對于深入理解激光增材制造材料的成形機制及性能提升機制具有重要作用。而從“多相材料”躍升至“多材料”(mulTiplemateriAlS)增材制造,則是在同一個成形構件內部的不同位置布局不同的打印材料,真正實現將“合適的材料添加到合適的位置”,以應對構件不同部位的性能/功能需求。這對激光增材制造的裝備和工藝提出了變革性要求,打印裝備中的粉末輸運系統、鋪粉系統、粉末搜集系統及對應的軟件控制系統均需重新設計,以應對多材料打印的需求。同時,在打印工藝上,多材料布局依賴于對激光增材制造工藝更為精準的微/宏觀跨尺度調控與優化。
3)基于激光增材制造創新結構設計,實現構件的高性能化和多功能化,以凸顯“獨特的結構實現獨特的功能”。隨著激光增材制造技術的日臻成熟,特別是面向航空航天領域的嚴苛的服役環境需求,成形材料及構件的力學性能已不再是唯一的追求目標,實現材料/構件的多功能化正成為重要的發展趨勢。借助增材制造技術的復雜結構和多材料一體化成形能力,通過仿生結構、拓撲優化結構、超材料、超結構等創新結構設計,有望實現增材制造材料/構件在光、聲、熱、電、磁等功能領域的突破,甚至是顛覆。激光增材制造創新結構設計、多功能設計、多材料布局、工藝精準調控是構件實現材料-結構-功能一體化的重要方向?;诙辔锢韴龅臄抵的M仿真,融合機器學習、數字孿生等新興的人工智能技術,可為功能化材料/結構的設計與優化提供理論指導;多材料打印、微/宏觀大跨尺度結構打印、多工藝混合多進程打印等創新增材制造技術的研發,可為功能化材料/結構的成形提供技術支撐。
4)面向全尺寸構件和全工藝流程的激光增材制造工藝仿真、監測及優化關鍵技術與方法。激光增材制造數值仿真需要考慮高能激光輻照下非平衡熔池內多相能量、動量和質量的多形式物理冶金行為,當前的數值仿真物理模型普遍為成形數道或數層的計算當量,需進一步拓寬至全尺寸構件級成形過程的熱場、流場、相場和應力場的調控研究,進而需進一步合理匹配物理模型的準確性和計算效率。另一方面,需基于數值仿真方法研究增材制造構件結構特征、成形工藝、成形環境對成形質量和成形穩定性的影響規律,實現對成形質量、成形效率及潛在的成形風險等問題的預判。未來在航空航天等領域的增材制造技術研究與應用方面,應建立成形構件的材料數據、模型數據、工藝策略數據庫等仿真數字平臺與成形設備、成形過程監控等成形平臺的數字孿生集成化,實現成形構件虛擬制造評估與生產過程仿真評估;通過機器學習建立成形設備參數、過程監控與監測指標評判方法,為激光增材制造工藝優化、成形質量提升、制造穩定性調控提供預判方法及現場技術支撐。
相關鏈接