前言
激光加工技術(shù)作為一種先進(jìn)的加工手段,在現(xiàn)代航空航天、國(guó)防領(lǐng)域以及國(guó)家建設(shè)中扮演著越來(lái)越重要的角色。特別是在鈦合金加工領(lǐng)域,2000年以后,隨著高功率激光器品質(zhì)的不斷提升,激光焊接與激光增材制造的應(yīng)用越發(fā)廣泛。本文在研究國(guó)內(nèi)外激光加工技術(shù)相關(guān)文獻(xiàn)報(bào)道的基礎(chǔ)上,對(duì)激光焊接和激光增材制造在鈦合金航空結(jié)構(gòu)件加工中的應(yīng)用現(xiàn)狀進(jìn)行總結(jié)分析。隨著航空結(jié)構(gòu)件向大型整體化、構(gòu)型拓?fù)浠⒔Y(jié)構(gòu)功能一體化的不斷發(fā)展,未來(lái)激光加工技術(shù)在鈦合金結(jié)構(gòu)件加工領(lǐng)域的應(yīng)用場(chǎng)景將更為廣泛,同時(shí)也對(duì)未來(lái)鈦合金激光加工成套設(shè)備也提出了更高要求,不受制于人的高端激光成套制造設(shè)備將是鈦合金航空結(jié)構(gòu)件加工核心競(jìng)爭(zhēng)力。
1、軍機(jī)結(jié)構(gòu)件制造面臨的挑戰(zhàn)及發(fā)展趨勢(shì)
1.1 各代軍機(jī)結(jié)構(gòu)需求及材料發(fā)展
一代軍機(jī),一代材料[1]。第一代飛機(jī)主要滿(mǎn)足高亞音速飛行,強(qiáng)調(diào)結(jié)構(gòu)件的屈服強(qiáng)度、抗拉強(qiáng)度、塑性及沖擊韌性,主要使用鋼骨架和木質(zhì)材料;第二代飛機(jī)主要滿(mǎn)足高空高速、近距格斗需求,強(qiáng)調(diào)關(guān)鍵部位的疲勞性能,大量使用鋁合金和鋼;第三代飛機(jī)主要滿(mǎn)足高亞聲速機(jī)動(dòng)性需求,關(guān)鍵部位的材料要求具有較高的損傷容限性能,要求材料具有
較低的裂紋擴(kuò)展速率和斷裂韌度,需要應(yīng)用大量輕質(zhì)高性能材料,在鋁合金和鋼的基礎(chǔ)上,增加了鈦合金與復(fù)合材料的使用;第四代飛機(jī)主要強(qiáng)調(diào)隱身性能和長(zhǎng)壽命周期,注重飛機(jī)的耐久性設(shè)計(jì),主要材料與三代機(jī)相近,但鈦合金與復(fù)合材料占比更大;第五代飛機(jī)需要具備高智能、高協(xié)同、高速飛行的特性,對(duì)結(jié)構(gòu)強(qiáng)度要求更高,還需應(yīng)用大量熱防護(hù)材料和耐高溫合金。
1.2 軍機(jī)結(jié)構(gòu)件制造面臨的挑戰(zhàn)
1.2.1 減重增壽
機(jī)體結(jié)構(gòu)是決定軍機(jī)性能指標(biāo)關(guān)鍵要素之一,半個(gè)世紀(jì)以來(lái),結(jié)構(gòu)技術(shù)一直在發(fā)展,結(jié)構(gòu)形式已趨于“經(jīng)典”[2]。如表 1 所示,國(guó)外各代戰(zhàn)機(jī)機(jī)體結(jié)構(gòu)重量占全機(jī)重量百分比不斷降低,機(jī)體疲勞壽命需求在不斷增長(zhǎng)。但相較于理想結(jié)構(gòu)重量,F(xiàn)35A超重 640 kg,F(xiàn)35B超重 900 kg,近期美國(guó)投入 3.5 億美元對(duì) 162 架四代飛機(jī)進(jìn)行抗疲勞結(jié)構(gòu)改進(jìn)。減重增壽仍然是軍機(jī)結(jié)構(gòu)件制造面臨的主要挑戰(zhàn)。

1.2.2 低成本、快速制造
快速制造和低成本制造是戰(zhàn)機(jī)工業(yè)化生產(chǎn)的核心。現(xiàn)有的結(jié)構(gòu)件制造工藝,材料利用率極低,部分結(jié)構(gòu)零件材料去除率達(dá) 90%以上;復(fù)雜結(jié)構(gòu)件加工工序多,生產(chǎn)周期長(zhǎng)。簡(jiǎn)化制造工藝,提升加工效率,提高原材料利用率,既滿(mǎn)足國(guó)家“雙碳”發(fā)展新形勢(shì)的需求,也符合航空制造業(yè)的根本利益。
1.3 軍機(jī)結(jié)構(gòu)件制造發(fā)展趨勢(shì)
1.3.1 結(jié)構(gòu)大型化、整體化
目前的機(jī)體結(jié)構(gòu)采用以小拼大的方式通過(guò)連接件完成連接[3],該方式直接導(dǎo)致了機(jī)體結(jié)構(gòu)超重,疲勞薄弱環(huán)節(jié)多,開(kāi)裂頻發(fā)。對(duì)于飛機(jī)結(jié)構(gòu)件,將傳統(tǒng)裝配結(jié)構(gòu)進(jìn)行一體化設(shè)計(jì)并完成制造,既減少了結(jié)構(gòu)件和連接件的數(shù)量,又能有效消除分離面,減少冗余結(jié)構(gòu),減緩應(yīng)力集中,減少疲勞薄弱環(huán)節(jié)。
結(jié)構(gòu)大型化、整體化設(shè)計(jì),突破了原有機(jī)體設(shè)計(jì)極限,能夠?qū)崿F(xiàn)機(jī)體結(jié)構(gòu)減重 20%以上,力學(xué)薄弱環(huán)節(jié)預(yù)計(jì)減少 30%以上,有效提升機(jī)體壽命。同時(shí),整體化結(jié)構(gòu)簡(jiǎn)化了機(jī)體裝配工裝與工藝,機(jī)體制造周期預(yù)計(jì)縮短30%以上。
1.3.2 結(jié)構(gòu)構(gòu)型拓?fù)浠?/p>
用仿生拓?fù)錁?gòu)型代替?zhèn)鹘y(tǒng)的縱橫加筋板構(gòu)型,材料根據(jù)傳力路徑和功能需求布局,能將材料布置到最優(yōu)傳力路徑,實(shí)現(xiàn)“無(wú)冗余”設(shè)計(jì),進(jìn)一步優(yōu)化了結(jié)構(gòu)設(shè)計(jì),實(shí)現(xiàn)減重。圖 1 為拓?fù)鋬?yōu)化前后的飛機(jī)結(jié)構(gòu)零件,零件質(zhì)量由 0.89 kg 減至 0.35 kg,減重60.6%。
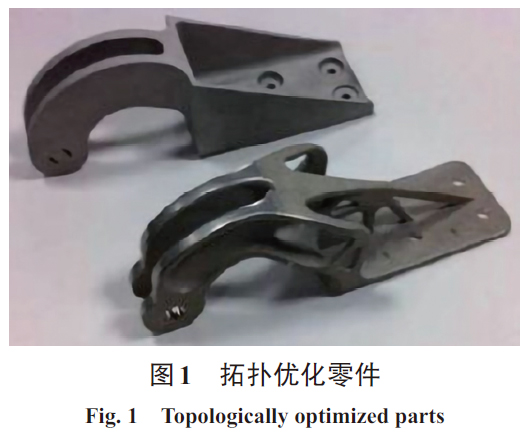
1.3.3 結(jié)構(gòu)功能一體化
目前,軍機(jī)的結(jié)構(gòu)系統(tǒng)與功能系統(tǒng)是獨(dú)立的,未來(lái)的軍機(jī)會(huì)將功能系統(tǒng)融入結(jié)構(gòu)中,取消功能系統(tǒng)的冗余,功能結(jié)構(gòu)一體化,諸如防熱材料、微結(jié)構(gòu)與結(jié)構(gòu)構(gòu)型融合,達(dá)到耐熱防熱的目的,可進(jìn)一步實(shí)現(xiàn)減重。典型防熱承載一體化結(jié)構(gòu)如圖 2 所示。
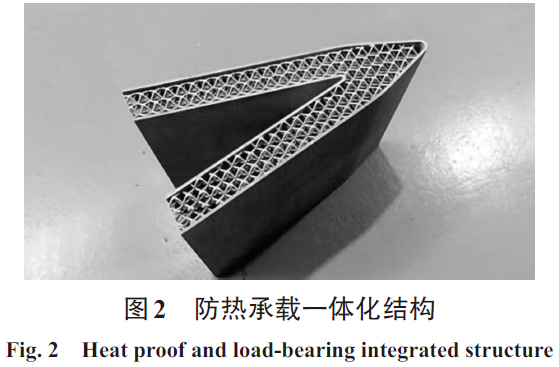
2、激光加工技術(shù)在鈦合金航空結(jié)構(gòu)件制造中的應(yīng)用現(xiàn)狀
2.1 激光焊接技術(shù)
激光焊接在航空結(jié)構(gòu)件制造的優(yōu)勢(shì)主要有兩點(diǎn)[4-5]:首先,焊接代替?zhèn)鹘y(tǒng)鉚接,節(jié)省了大量鉚釘,能有效實(shí)現(xiàn)減重;其次,整體焊縫的強(qiáng)度優(yōu)于多個(gè)鉚釘連接的強(qiáng)度。如圖 3 所示,鈦合金焊縫及其熱影響區(qū)的強(qiáng)度均大于母材,整體焊縫的強(qiáng)度非常優(yōu)秀,能夠有效增長(zhǎng)機(jī)體疲勞壽命。
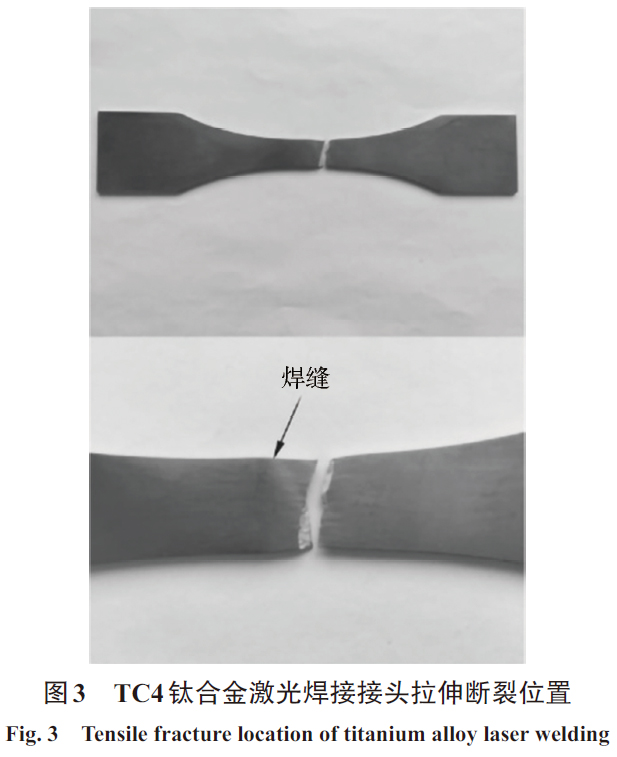
目前應(yīng)用最為廣泛和成熟的是T型接頭雙光束激光焊技術(shù),該技術(shù)最早由空客于 2000 年應(yīng)用于A318 系列飛機(jī)的下機(jī)身蒙皮焊接(見(jiàn)圖 4),被公認(rèn)為近十年大型客機(jī)制造領(lǐng)域的一次技術(shù)革命,改變了焊接技術(shù)不適用于飛機(jī)制造的傳統(tǒng)觀念。國(guó)內(nèi)針對(duì)TC4 鈦合金和TA15 鈦合金激光焊接已進(jìn)行了系統(tǒng)的研究[6-10],激光焊接已經(jīng)應(yīng)用于我國(guó)某些型號(hào)飛機(jī)的鈦合金腹鰭制造、鈦合金蒙皮拼焊、壁板與長(zhǎng)桁T型接頭焊接等,配套制造設(shè)備也較為成熟。
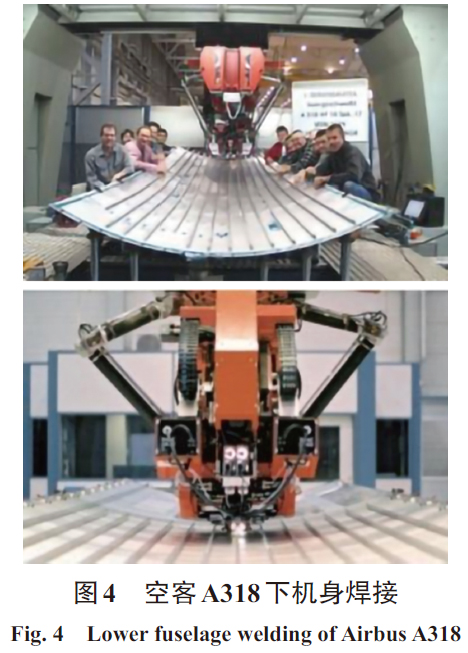
圖 5 為中國(guó)商飛雙光束同步焊接設(shè)備,用于國(guó)產(chǎn)某客機(jī)制造。此外,北京航空制造工程研究所已將激光焊接技術(shù)應(yīng)用于發(fā)動(dòng)機(jī)鈦合金承力構(gòu)件制造。
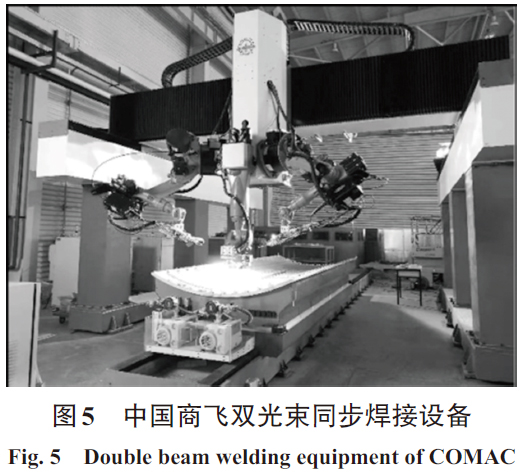
在鈦合金承力結(jié)構(gòu)件上,激光焊接技術(shù)即將開(kāi)展深入應(yīng)用,特別是鈦合金原位激光焊接。原位焊接技術(shù)屬于近凈成形技術(shù)領(lǐng)域,是指零件成型后,僅需少量加工或不再加工,就可作為機(jī)械構(gòu)件的成型技術(shù)。原位焊接技術(shù)是美國(guó)首次在 F-22 戰(zhàn)機(jī)上提出并應(yīng)用的,利用高能束流對(duì)裝配體實(shí)施焊接,焊接后無(wú)需進(jìn)行二次機(jī)械加工,實(shí)現(xiàn)了飛機(jī)骨架零件原位焊接工藝與裝配技術(shù)的協(xié)調(diào)統(tǒng)一,代替?zhèn)鹘y(tǒng)鉚接,大幅減重并縮短部件制造周期。F-22 在研發(fā)階段,受制于當(dāng)時(shí)激光功率,鈦合金后機(jī)身大量采用電子束焊接。先由 3~4 個(gè)片段縱向焊接組成盒狀段,再由盒裝段焊接成框,最后焊接為整體艙段,如圖 6 所示,鈦合金焊縫總長(zhǎng)度約 9m,質(zhì)量相比于機(jī)械連接減少 182 kg[11]。目前,原位焊接技術(shù)在國(guó)內(nèi)
航空制造領(lǐng)域尚無(wú)工程應(yīng)用,鈦合金結(jié)構(gòu)件的原位激光焊接的應(yīng)用將是未來(lái)極具價(jià)值的研究方向。
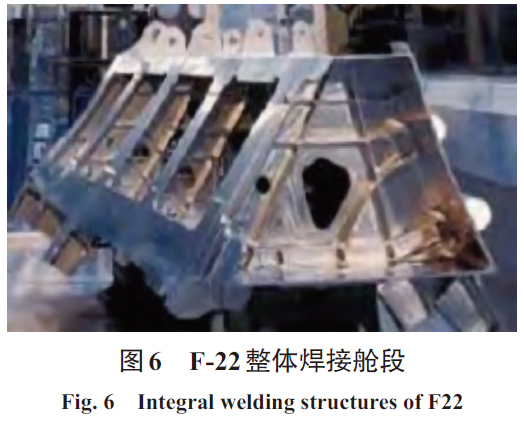
未來(lái),激光焊接在航空結(jié)構(gòu)件制造領(lǐng)域的發(fā)展趨勢(shì),是焊接更為復(fù)雜的機(jī)體結(jié)構(gòu)和新材料,進(jìn)一步實(shí)現(xiàn)機(jī)體減重增壽。此外,航空結(jié)構(gòu)件自身價(jià)值較高,保證加工質(zhì)量至關(guān)重要,由此帶來(lái)的挑戰(zhàn)主要有以下幾個(gè)方面:
(1)激光焊接頭可達(dá)性拓展。
復(fù)雜鈦合金機(jī)體框架結(jié)構(gòu)的定位和夾持工裝相互交錯(cuò),對(duì)激光焊接頭的可達(dá)性造成極大干擾。
一方面,需要合理規(guī)劃焊接路徑,優(yōu)化工裝設(shè)計(jì),保持操作空間的最大開(kāi)敞性。另一方面,需要開(kāi)展專(zhuān)用焊接頭的研發(fā),具備小型化、遠(yuǎn)距焊接、末端位姿可調(diào)等要素。
(2)變形控制。
變形控制包括焊接變形控制和熱處理變形控制。需進(jìn)一步開(kāi)展焊接對(duì)象焊接工藝試驗(yàn),完成最佳的焊接策略匹配,實(shí)現(xiàn)焊接變形控制最優(yōu)解的同時(shí)保證焊接可靠性。需要進(jìn)一步開(kāi)展熱處理變形機(jī)理研究,設(shè)計(jì)出合理的保形工裝和熱處理策略來(lái)實(shí)現(xiàn)復(fù)雜部件的熱處理變形控制。此外,還需要探索新型的熱處理方式,諸如超聲沖擊、激光沖擊等特種工藝來(lái)消除焊接應(yīng)力。
(3)新材料焊接。
針對(duì)未來(lái)超高速飛行器對(duì)耐溫材料的需求,需進(jìn)一步開(kāi)展高溫鈦合金和熱塑性復(fù)合材料的激光焊接工藝研究,并進(jìn)行力學(xué)性能和疲勞性能考核,為后續(xù)新材料工程化應(yīng)用提供支撐。
2.2 激光增材制造技術(shù)
激光選區(qū)熔化(Selective LaserMelting,SLM)、激光直接沉積(Laser MeltingDeposition,LMD)是目前主要的鈦合金激光增材制造工藝[12]。航空結(jié)構(gòu)件具有多品種、小批量的特點(diǎn),結(jié)構(gòu)越復(fù)雜,增材制造的成本和效率優(yōu)勢(shì)相比傳統(tǒng)制造方法就越明顯。
SLM技術(shù)分層層厚較小(30~60 μm),可直接快速成型終端金屬產(chǎn)品,尺寸精度高,表面質(zhì)量好,可實(shí)現(xiàn)任意復(fù)雜零部件的高效致密成形,特別適合內(nèi)部有復(fù)雜異形結(jié)構(gòu)且用傳統(tǒng)方法無(wú)法制造的復(fù)雜零部件。
通用電氣公司專(zhuān)注于增材制造以降低其發(fā)動(dòng)機(jī)制造成本,采用SLM技術(shù)已完成大量零部件的批量制造。圖 7 為航空發(fā)動(dòng)機(jī)燃油噴嘴,將 20個(gè)零件集成為 1 個(gè)部件進(jìn)行打印,減重 25%,已實(shí)現(xiàn)數(shù)萬(wàn)個(gè)部件的批量制造。此外,空客通過(guò)基于有限元分析的結(jié)構(gòu)優(yōu)化應(yīng)用于現(xiàn)有零部件的再設(shè)計(jì),采用SLM技術(shù)實(shí)現(xiàn)了大幅減重,如圖8所示。
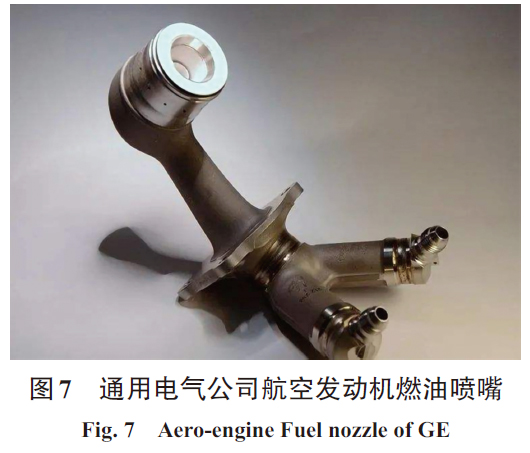
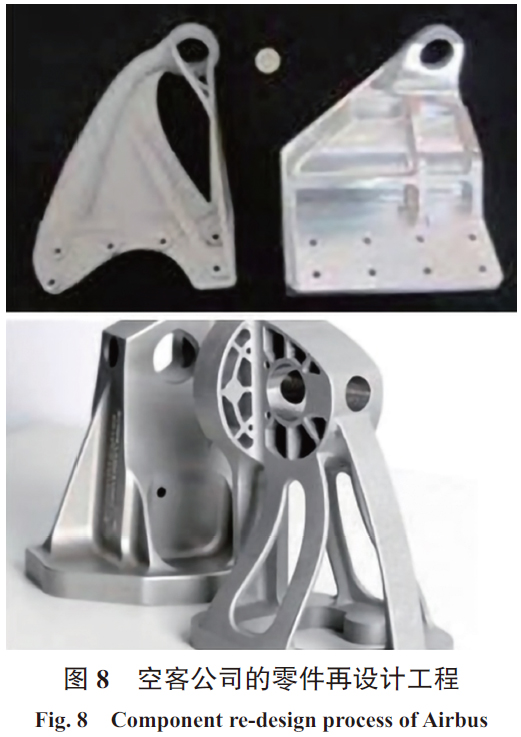
未來(lái)軍機(jī)將具有超高速飛行的特征,熱防護(hù)技術(shù)是未來(lái)飛機(jī)結(jié)構(gòu)件的關(guān)鍵技術(shù)之一,防熱承載結(jié)構(gòu)具有多孔、點(diǎn)陣等特征,且內(nèi)部需要微流道完成主動(dòng)散熱,此類(lèi)結(jié)構(gòu)傳統(tǒng)工藝無(wú)法完成加工。通用航空公司設(shè)計(jì)的內(nèi)置流道的航空發(fā)動(dòng)機(jī)葉片如圖 9所示,飛機(jī)用金屬多功能點(diǎn)陣結(jié)構(gòu)如圖 10 所示,可實(shí)現(xiàn)結(jié)構(gòu)承載、防熱、隱身等功能的融合。此類(lèi)結(jié)構(gòu)傳統(tǒng)工藝無(wú)法完成加工,SLM技術(shù)恰好能夠滿(mǎn)足相關(guān)制造需求。
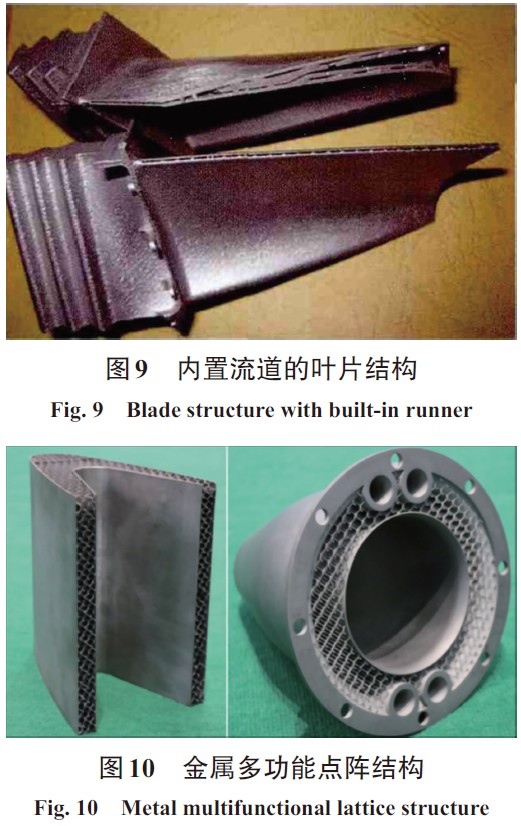
鈦合金防熱承載一體化結(jié)構(gòu)的激光選區(qū)熔化成型應(yīng)用將是未來(lái)極具價(jià)值的研究方向。
在 SLM 設(shè)備制造領(lǐng)域,以美國(guó) Optomec、德國(guó)EOS、西安鉑力特、南京中科煜宸等為代表的多家單位均已研發(fā)出工業(yè)級(jí) SLM 設(shè)備,國(guó)內(nèi)外典型 SLM設(shè)備主要特性如表2所示。
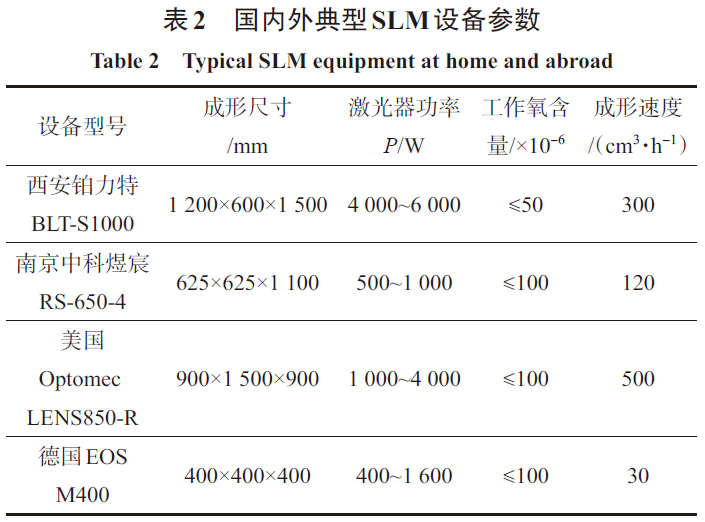
其中,西安鉑力特增材技術(shù)股份有限公司于2022 年 5 月 推出了 12 激 光 SLM 3D 打 印機(jī) BLT-S1000,目前處于國(guó)內(nèi)領(lǐng)先水平,如圖 11 所示。其成型尺寸可達(dá)1200 mm×600 mm×1 500 mm,可實(shí)現(xiàn)大尺寸復(fù)雜結(jié)構(gòu)件的一體成型,最大成型速率可達(dá)300 cm3/h。提升鋪粉設(shè)備的加工效率仍將是未來(lái)極具價(jià)值的研究方向。
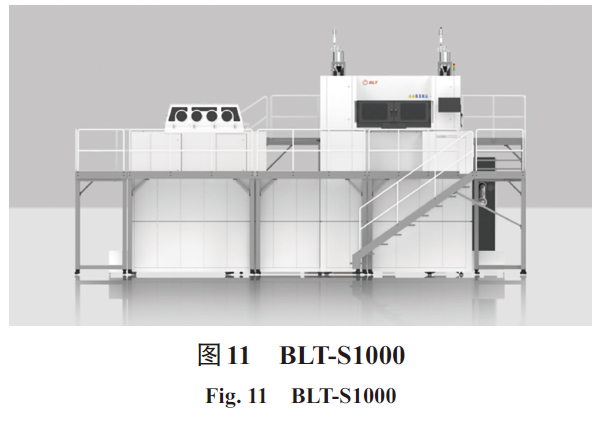
激光直接沉積技術(shù)(LMD)具有材料利用率高、機(jī)加工量小、制造周期短的特點(diǎn),同軸送粉的工藝特點(diǎn)決定其成形尺寸不受限制,可以實(shí)現(xiàn)同一構(gòu)件上多材料的復(fù)合和梯度制造,適用于大型結(jié)構(gòu)件或者結(jié)構(gòu)不是特別復(fù)雜的功能性零件的加工制造。
LMD技術(shù)在國(guó)內(nèi)外航空航天領(lǐng)域得到了廣泛的應(yīng)用,例如波音公司、空客公司、洛克希德馬丁公司、GE航空等世界著名的航空公司都在大力發(fā)展各自的激光直接沉積技術(shù)[13]。北京航空航天大學(xué)研制的某大型激光直接沉積金屬增材制造設(shè)備如圖 12所示,可為中國(guó)商用飛機(jī)、軍機(jī)項(xiàng)目制造大型復(fù)雜部件,包括鈦機(jī)身骨架及高強(qiáng)度起落架。北航王華明教授團(tuán)隊(duì)研制了主承力飛機(jī)鈦合金加強(qiáng)框等關(guān)鍵構(gòu)件,實(shí)現(xiàn)了在包括C919 大型客機(jī)在內(nèi)的多種型號(hào)飛機(jī)上的裝機(jī)應(yīng)用。北航應(yīng)用LMD技術(shù)制造出了飛機(jī)大型鈦合金主承力構(gòu)件,如圖 13 所示。西北工業(yè)大學(xué)采用LMD技術(shù)成功試制了C919 機(jī)翼肋構(gòu)件,如圖14所示。
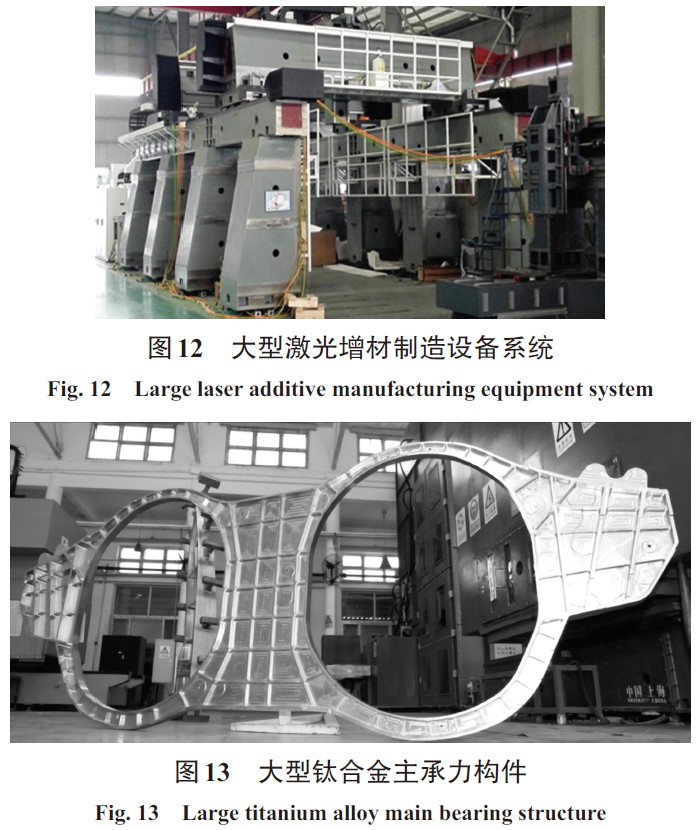
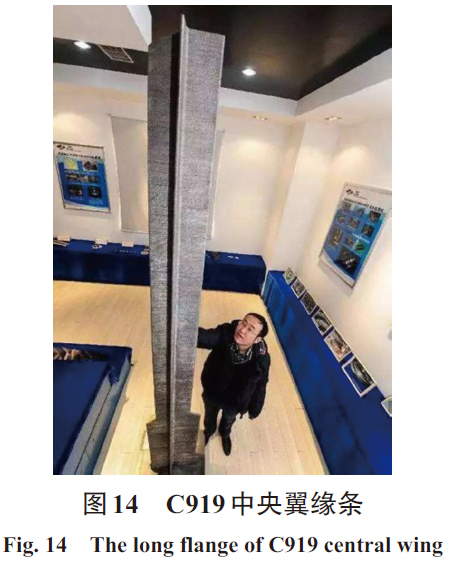
在LMD設(shè)備制造領(lǐng)域,以美國(guó) EFESTO、德國(guó)EOS、西安鉑力特、南京中科煜宸、鑫精合激光等為代表的多家企業(yè)均已研發(fā)出工業(yè)級(jí)LMD設(shè)備,國(guó)內(nèi)外典型LMD設(shè)備主要參數(shù)如表3所示。

南京中科煜宸研發(fā)的大型智能化雙光束裝備性能指標(biāo)達(dá)到國(guó)際先進(jìn)、國(guó)內(nèi)領(lǐng)先的水平,如圖 15所示,是國(guó)際上首次提出采用雙萬(wàn)瓦級(jí)激光同步送粉打印技術(shù),沉積速度可達(dá) 700 cm3/h,設(shè)備剛性成型尺寸可達(dá) 4 m×3.5 m×3
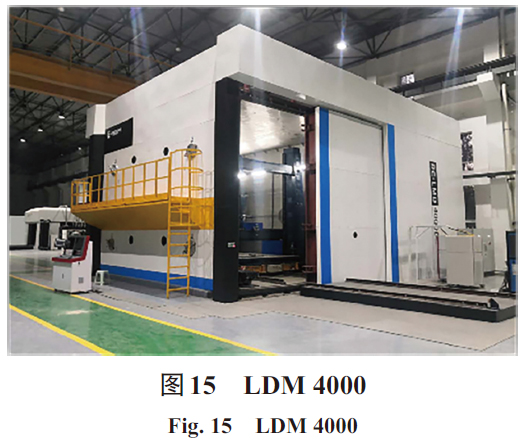
m,柔性成型尺寸達(dá) 13 m×3.5 m×3 m,加工能力覆蓋了目前航空鈦合金主承力結(jié)構(gòu)件的所有門(mén)類(lèi),滿(mǎn)足未來(lái)型號(hào)及特殊構(gòu)件制造需求。此外,航空工業(yè)成飛集團(tuán)也研制了大型LMD同軸送粉設(shè)備,并實(shí)現(xiàn)了飛機(jī)增材制造工程化應(yīng)用。降低設(shè)備加工使用成本將是LMD設(shè)備未來(lái)的研究方向。大型構(gòu)件的應(yīng)力控制和變形開(kāi)裂是LMD技術(shù)面臨的關(guān)鍵難題。
激光增材制造在航空結(jié)構(gòu)件制造領(lǐng)域的未來(lái)發(fā)展趨勢(shì),將是進(jìn)一步拓寬應(yīng)用面,提高零部件力學(xué)性能,加工對(duì)象將由機(jī)體非承力件和次承力件向主承力件進(jìn)一步拓展。同時(shí),進(jìn)一步提升加工工藝成熟度,降低加工成本,更有助于該技術(shù)的工程化應(yīng)用。由此帶來(lái)的挑戰(zhàn)主要有以下幾個(gè)方面:
(1)提升正向設(shè)計(jì)能力。
目前,增材制造技術(shù)主要還是對(duì)傳統(tǒng)鑄造、鍛造技術(shù)的替代,沒(méi)有完全發(fā)揮其高設(shè)計(jì)自由度的優(yōu)勢(shì),需要進(jìn)一步提升結(jié)構(gòu)件設(shè)計(jì)能力,在設(shè)計(jì)中融合增材的思想,通過(guò)正向設(shè)計(jì)的理念,從源頭上實(shí)現(xiàn)結(jié)構(gòu)設(shè)計(jì)上的顛覆性創(chuàng)新。
(2)提高零件力學(xué)性能。
激光增材制造的關(guān)鍵要求之一是獲得所需的力學(xué)性能,需要進(jìn)一步優(yōu)化打印工藝,減少變形,避免開(kāi)裂,提高力學(xué)性能。一方面,需要開(kāi)展大量的基礎(chǔ)性試驗(yàn),建立工藝數(shù)據(jù)庫(kù);另一方面,需要開(kāi)發(fā)可靠的預(yù)測(cè)性過(guò)程模型,諸如過(guò)程熱模型、微結(jié)構(gòu)預(yù)測(cè)模型和力學(xué)性能預(yù)測(cè)模型等,提升加工過(guò)程的可靠性。
(3)健全基礎(chǔ)性能數(shù)據(jù)體系。
作為一項(xiàng)正在迅速發(fā)展的高新技術(shù),增材制造在原材料、工藝、后處理、組織性能數(shù)據(jù)庫(kù)等方面的數(shù)據(jù)儲(chǔ)備還不充足,需要業(yè)界共同努力,健全激光增材制造金屬材料的基礎(chǔ)性能數(shù)據(jù)體系,共同開(kāi)發(fā)出增材制造粉末原材料、工藝過(guò)程等規(guī)范。
3、激光加工設(shè)備在鈦合金航空結(jié)構(gòu)件制造的應(yīng)用展望
伴隨著鈦合金激光加工技術(shù)在我國(guó)航空結(jié)構(gòu)件制造中的應(yīng)用越來(lái)越廣泛,鈦合金激光加工成套設(shè)備同樣面臨著壓力與挑戰(zhàn),需要進(jìn)一步完善和發(fā)展,提升激光加工設(shè)備競(jìng)爭(zhēng)力。
3.1 成套系統(tǒng)多功能化
高效低成本制造、近凈成形將是未來(lái)鈦合金航空結(jié)構(gòu)件制造發(fā)展方向。航空工業(yè)屬于典型的離散制造,現(xiàn)行的工藝以及加工設(shè)備大多僅具備單一的加工功能,零件在不同的工藝節(jié)點(diǎn)周轉(zhuǎn),降低了加工效率。單個(gè)離散點(diǎn)多功能化,簡(jiǎn)化工藝流程,需要未來(lái)的高端激光制造集成系統(tǒng)向多功能化發(fā)展,將激光制造精細(xì)、直接近凈成形的優(yōu)點(diǎn)與傳統(tǒng)制造技術(shù)結(jié)合起來(lái),形成最佳的制造策略,諸如增材、焊接、減材、在線測(cè)量一體化的自動(dòng)設(shè)備。同時(shí),研發(fā)面向原位自適應(yīng)制造的專(zhuān)用新設(shè)備,諸如在線焊接變形測(cè)量和分析設(shè)備、在線焊接氣孔檢測(cè)設(shè)備、原位去應(yīng)力設(shè)備,可有效減少后續(xù)加工及檢測(cè)工序。
3.2 加工過(guò)程智能化
智能化的激光加工系統(tǒng)將有效提高加工效率,保證加工質(zhì)量,降低對(duì)操作人員的要求。將智能傳感器、數(shù)字總線技術(shù)等智能部件融入激光加工設(shè)備,通過(guò)對(duì)生產(chǎn)全過(guò)程實(shí)時(shí)在線檢測(cè)、閉環(huán)過(guò)程控制來(lái)確保激光加工的加工質(zhì)量、一致性和再現(xiàn)性。
諸如基于視覺(jué)測(cè)量、激光測(cè)量的智能末端,完成部件裝配的間隙與階差的自動(dòng)測(cè)量,確保裝配狀態(tài),代替現(xiàn)有人工測(cè)量;高精度的遠(yuǎn)距窄焊縫的焊縫跟蹤末端,滿(mǎn)足航空結(jié)構(gòu)件形狀復(fù)雜、夾具復(fù)雜、焊接末端可達(dá)性較差的特殊焊接場(chǎng)景需求;具備高溫加工全過(guò)程監(jiān)測(cè)并結(jié)合 AI 深度學(xué)習(xí)功能的熔池監(jiān)測(cè)設(shè)備,實(shí)現(xiàn)過(guò)程中的關(guān)鍵工藝參數(shù)和在線實(shí)時(shí)監(jiān)測(cè)、反饋閉環(huán)控制;另外,構(gòu)建激光加工知識(shí)工程,形成激光加工設(shè)備技術(shù)管控平臺(tái),也能有效提升激光加工的可靠性及智能化程度。
3.3 配套系統(tǒng)高效化
鈦合金在高溫下非常活躍,在 300 ℃以上極易與氫反應(yīng),600 ℃以上極易與氧反應(yīng),700 ℃以上極易與氮反應(yīng),須施加氬氣保護(hù),高質(zhì)量的氣體保護(hù)措施能有效保障鈦合金加工質(zhì)量,提升零部件制造合格率并降低加工成本。對(duì)于傳統(tǒng)保護(hù)夾具吹氣的方式,需注重其保護(hù)的可靠性,同時(shí)需降低對(duì)光束可達(dá)性的影響;對(duì)于整體密封保護(hù)的方式,需進(jìn)一步提高箱體密封性,優(yōu)化惰性氣體置換和凈化過(guò)程氣流組織,降低惰性氣氛建立時(shí)間,提高加工效率。
3.4 核心部件自主化
經(jīng)過(guò)多年的不懈努力,我國(guó)激光制造設(shè)備已實(shí)現(xiàn)“從無(wú)到有”,目前正處于“從有到好”的階段。但部分高端核心部件目前仍然處于受制于人的局面,急需研發(fā)高功率、高可靠性的國(guó)產(chǎn)激光器,并針對(duì)性地改善功率衰減過(guò)快的缺點(diǎn)。研發(fā)高功率、高精度、高可靠性國(guó)產(chǎn)激光焊接頭/打印頭,在線熔池監(jiān)測(cè)裝置等核心部件,提升高端激光成套制造設(shè)備的
自主化程度。
4 、結(jié)論
以航空結(jié)構(gòu)件制造為背景,介紹了航空結(jié)構(gòu)件制造面臨的挑戰(zhàn)與發(fā)展趨勢(shì),綜述了激光加工技術(shù)在鈦合金航空結(jié)構(gòu)件制造中的應(yīng)用現(xiàn)狀,并對(duì)鈦合金激光加工成套設(shè)備的未來(lái)發(fā)展方向提出了相關(guān)建議。
(1)分析了軍機(jī)結(jié)構(gòu)件制造面臨的挑戰(zhàn)和發(fā)展方向。
(2)介紹了激光焊接技術(shù)、激光增材制造技術(shù)在飛機(jī)結(jié)構(gòu)件制造中的應(yīng)用現(xiàn)狀及前景,對(duì)激光技術(shù)在軍機(jī)結(jié)構(gòu)件制造的應(yīng)用具有指導(dǎo)價(jià)值。
(3)基于未來(lái)軍機(jī)快速、高效、低成本制造的考慮,對(duì)未來(lái)鈦合金激光加工成套設(shè)備技術(shù)的發(fā)展,提供了方向和發(fā)展建議。
參考文獻(xiàn):
[1] 李航航,閻勇,尹航 . 戰(zhàn)斗機(jī)新結(jié)構(gòu)應(yīng)用與新材料需求分析[J]. 航空科學(xué)技術(shù),2020,31(4):8-13.
Li Hanghang,YanYong,YinHang. New structureapplication andnewmaterialrequirementanalysisfor fighter aircraft[J]. Aeronautical science&Technology,
2020,31(4):8-13.
[2] 劉文珽 . 結(jié)構(gòu)可靠性設(shè)計(jì)手冊(cè)[M]. 北京:國(guó)防工業(yè)出版社,2008.
[3] 李蒙,鳳偉中,關(guān)蕾,等 . 航空航天緊固件用鈦合金材料綜述[J]. 有色金屬材料與程,2018,39(4):53-57.
Li Meng,F(xiàn)eng Weizhong,Guan Lei,et al. Review ontitanium alloymaterialsforaerospacefasteners[J]. Nonferrous MetalsMaterialsandEngineering,2018,39
(4):53-57.
[4] 許平,畢世權(quán),張偉寧,等 . 激光焊接大型整體壁板設(shè)計(jì)與考核方法[J].飛機(jī)設(shè)計(jì),2021,41(04):49-55.
XU Ping,BI Shiquan,ZHANG Weining,et al. Design and assessmentmethodoflaserweldedlargeintegral panel[J]. Aircraft Design,2021,41(04):49-55.
[5] 孫文君,王善林,陳玉華,等 . 鈦合金先進(jìn)焊接技術(shù)研究現(xiàn)狀[J]. 航空制造技術(shù),2019,62(18):63-72.
SUN Wenjun,WANGShanlin,CHEN Yuhua,et al. Development ofadvancedweldingtechnologiesfortitanium alloys[J]. Aeronautical ManufacturingTechnology,
2019,62(18):63-72.
[6] 李昊,陳潔,陳磊,等 . 雙光束激光焊接技術(shù)在民用飛機(jī)上的應(yīng)用現(xiàn)狀及發(fā)展[J]. 航空制造技術(shù),2012,55(21):50-53.
LI Hao,CHEN Jie,CHEN Lei,et al. Existing stateand development onduallaser-beambilateralweldingtech‐nology usedincivilaircraft[J]. Aeronautical Manufacturing Technology,2012,55(21):50-53.
[7] 龔時(shí)華,鄭忠香,王平江,等 . 十軸六聯(lián)動(dòng)雙光束激光焊接及其跟蹤控制技術(shù)[J]. 航空制造技術(shù),2018,61(11):34-39,47.
GONG Shihua,ZHENG Zhongxiang,WANGPingjiang,et al. Control technologyfordual-beamlaserwelding andseamtrackingwithten-axissix-linkageCNC
[J]. Aeronautical ManufacturingTechnology,2018,61(11):34-39,47.
[8] 蔣志偉,龔時(shí)華,王啟行 . 雙光束激光雙路焊接的跟蹤控制技術(shù)研究[J].激光技術(shù),2013,37(1):1-5.
JIANG Zhiwei,GONG Shihua,WANGQihang. Study on thetrackingcontroltechnologyofdual-beamlaser welding[J].Laser Technology,2013,37(1):1-5.
[9] 梁斌焱,許先雨,龔時(shí)華,等 . 三維 T 形焊縫的雙光束焊接及其焊縫跟蹤控制[J]. 焊接學(xué)報(bào),2016,37(2):47-50,131.
LIANG Binyan,XU Xianyu,GONG Shihua,et al.Dualbeam laserweldingandseamtrackingcontroltechnology for 3D T-beam[J]. TransactionsoftheChinaWelding
Institution,2016,37(2):47-50,131.
[10] 曹田野,徐志剛,王亞軍 . 雙光束激光焊機(jī)研究與設(shè)計(jì)[J].電焊機(jī),2016,46(1):40-44.
CAO Tianye,XU Zhigang,WANGYajun,et al. Research anddesignontheduallaser-beambilateral welder[J]. Electric WeldingMachine,2016,46(1):
40-44.
[11] 李志強(qiáng),陳瑋 . 高能束流加工技術(shù)在航空領(lǐng)域的應(yīng)用進(jìn)展[J].航空學(xué)報(bào),2022,43(04):54-66.
LI Zhiqiang,CHEN Wei.Application progressofpower beam processingtechnologyinaeronauticalindustry [J]. Acta AeronauticaetAstronauticaSinica,2022,43
(04):54-66.
[12] 林鑫,黃衛(wèi)東 . 應(yīng)用于航空領(lǐng)域的金屬高性能增材制造技術(shù)[J].中國(guó)材料進(jìn)展,2015,34(9):684-688,658.
LIN Xin,HUANG Weidong. High PerformanceMetal Additive ManufacturingTechnologyAppliedinAviation Fifield[J]. Materials China,2015,34(9):684-
688,658.
[13] 朱忠良,趙凱,郭立杰,等 . 大型金屬構(gòu)件增材制造技術(shù)在航空航天制造中的應(yīng)用及其發(fā)展趨勢(shì)[J]. 電焊機(jī),2020,50(1):1-14,124.
ZHU ZhongLiang,ZHAO Kai,GUO LiJie,et al. Application anddevelopmenttrendofadditivemanufacturing technologyoflarge-scalemetalcomponentinaerospace
manufacturing[J]. Electric WeldingMachine,2020,50(1):1-14.
相關(guān)鏈接